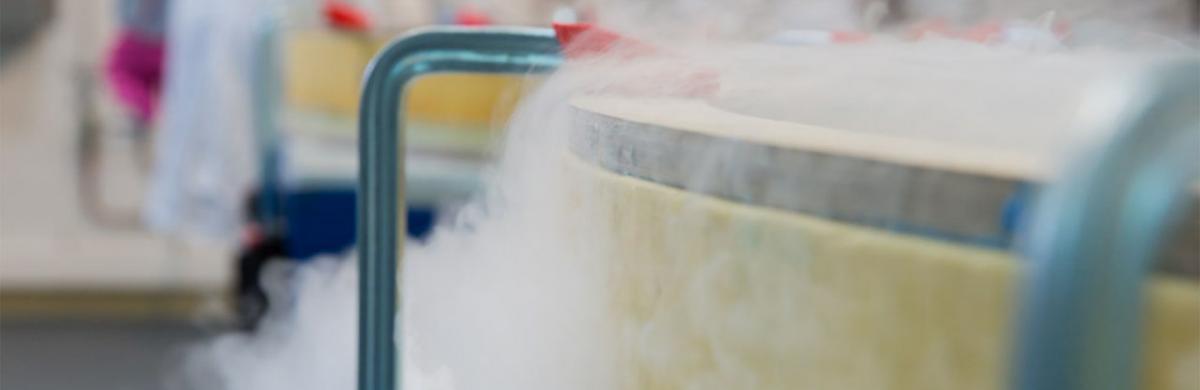
Delivering technological ambition
Our laboratories involve the efforts of around forty engineers, and we are engaged in the continual program of investment in new and upgraded facilities. As an intrinsically pioneering business, GTT places great importance on research and testing...
In the absence of actual data, it is essential to have the resources needed to maintain full control over all the challenges associated with our technologies. This is why GTT has its own research, test and approvals laboratories at its Saint-Rémy-lès-Chevreuse facility, which investigate and analyse the thermal and mechanical properties of materials and sub-assemblies, especially under cryogenic conditions. Because we are involved in developing new technologies, we have also developed special testing and trialing procedures, which, in conjunction with our significant thermodynamic modeling resources, have established our laboratories as a benchmark for the industry.
The range of measures includes static and semi-static testing, with particular focus on rupture, impact and fatigue testing. Our laboratories focus particularly on testing materials and bonding procedures by simulating the actual conditions encountered in shipyards (including environmental conditions), and the characteristics of materials in the accelerated aging phase. We use hexapod testing platforms of between 1 and 6 tons to analyze the full-scale effects of 'sloshing', the loads imposed on containment systems subject to the impact of moving liquids.
These sea swell simulators - a major challenge to this type of research work - make it possible to model the movement of the liquid in a tank on a small scale, but with millimeter-perfect linear precision. Each testing campaign normally runs for seven weeks, after which the data are analyzed as the basis for identifying those materials that respond most effectively to the mechanical demands measured during the testing phase. Models at 1/8th scale are also used to test containment systems under cryogenic conditions.
Although linked to high investment costs, these research and modeling facilities deliver many benefits, including the rapid availability and confidentiality of results, and greater innovation potential as a result of direct interactive contact between test teams and research teams. Another benefit of this organizational structure and its ability to promote internal knowledge is that every test is directly related to a particular project and the company's teams (35 of its 157 engineers work in the research laboratory), which means that the procedure is controlled from beginning to end, making the transport of LNG every bit as fascinating as aerospace and aviation.
High level equipment for research and tests
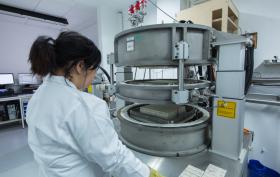
Associated document