The regulations require the LNG carriers owners to inspect all the tanks every 5 years regardless of their operational profile:
- IACS UR Z16 §2.2.1: All cargo tanks are to be examined internally.
- 2016 IGC Codes §1.4.2.2: A renewal survey at intervals specified by the Administration, but not exceeding five years.
The objective of the survey is to identify and eventually repair potential defects or damage on the Cargo Containment System (CCS), and the Pump Tower (PT). Such defects are generally associated with the liquid motion in the tanks.
In order to ensure the highest level of operational flexibility while meeting the safety standards, the CCS and the Pump Tower are designed according to North Atlantic conditions and worst low and high filling levels. However, the real life profile of the vessel is generally less severe, both from the sea conditions and the filling level standpoints.
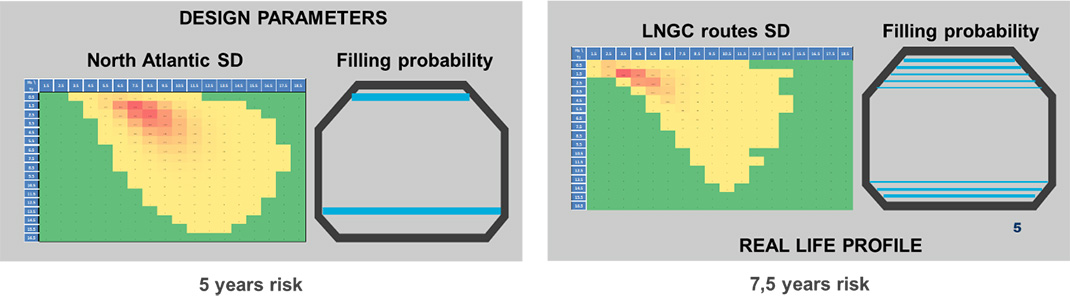
Thus, by monitoring the vessel’s real life profile, we can demonstrate, in many cases, that the five years damage risk considered under the design assumptions may be equivalent to the risk of a longer period (e.g. 7.5 years or even more) in actual operational conditions. This equivalence principle is a
permitted by the IGC code provided that it can be demonstrated with a proper risk assessment and mitigation plan. The overall process is subject to Flag approval.
From the financial, operational and ESG[1] points of view, the benefits of such an extension for the LNGc owners and the charters are numerous. Hence, a working group including GTT, ship owners, charterers, classification societies and Flag states defined a rigorous systematic process to build a survey extension dossier for an LNGc in order for the Flag to approve it. The process steps are:
- Hazard Identification (Owner / Class / GTT): Identify the key parameters / critical failure modes that require specific monitoring in view of extending inspection cycle.
- Risk Management:
- Build a justification dossier to demonstrate that the design can be validated for extended duration,
- Ensure that alternative methods can provide equivalent safety as for a conventional internal cargo tanks Survey,
- Establish recommendations and mitigation measures to minimize risks in accordance with As Low As Reasonably Practicable (ALARP) principle.
- Inspection Strategy
- Define an initial Inspection Strategy
- Define the logic to update this inspection plan
GTT has developed two innovative real time monitoring tools to support the continuous demonstration of the equivalence principle based on the actual vessel operational profile:
- Sloshing Virtual Sensors
- Cargo Tank Health Monitoring
With the Cargo Tank Health Monitoring, all the relevant parameters identified through a HAZID are monitored in real time. Any abnormal deviation is automatically detected by the supervisory rules in GTT Monitoring and Emergency Response Centre (HEARS) and double-checked by an officer on duty 24/7. If any risk is confirmed, the appropriate stakeholders are informed for immediate action.
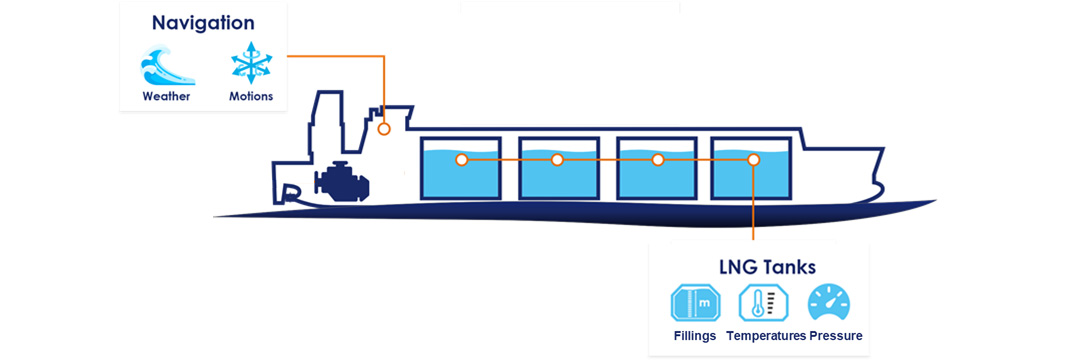
The Sloshing Virtual Sensor is a Machine Learning algorithm trained on model tests and numerical simulations. It makes the link between the tank motions, the filling levels and the loads on the CCS & the PT.
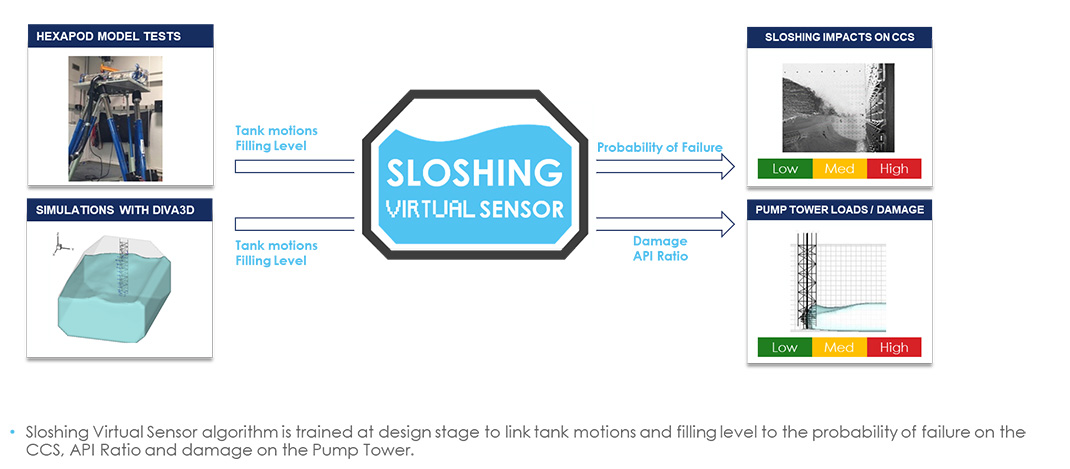
At sea, the application allows real-time monitoring of the cumulated damage on the PT and the Probability of Failure (PoF) of the CCS.
When design values are reached (equivalence principal) then appropriate stakeholders are informed to take appropriate action with regard to inspection plan defined during the risk assessment process.
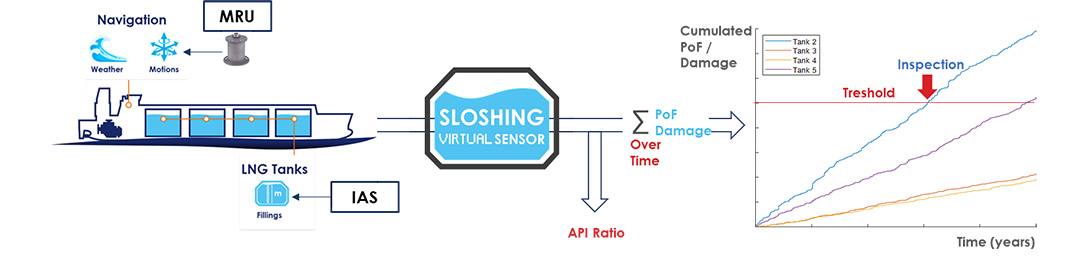
The Sloshing Virtual Sensor requires the installation on-board of 2 components:
- Motion Reference Unit (MRU) to measure the vessel motions
- Real Time Processing Server: to collect the MRU high frequency data, pre-process it, collect the cargo tank critical parameters, mainly from the Integrated Automation System (IAS), and send the data to the shore for real-time evaluation and monitoring.
[1] ESG = Environnemental, Social and Governance (non-financial KPIs)