Throughout over 60 years of experience in designing patented LNG membrane containment technologies, GTT has not only developed thorough engineering and design capabilities on its systems, but also specific on-site know-how that may be deployed during the construction process to the benefit of its clients, and industry stakeholders.
Benefiting from more than 10,600 cumulated tank-years for Mark III and more than 11,400 cumulated tank-years for NO96, GTT has also attended more than 1,100 refits where it was required to thoroughly scrutinize the cargo tanks. GTT is thus ready to mobilize an experienced team of surveyors to support the shipyard teams to ensure that the GTT systems are properly installed on board, and that the design specifications, drawings, studies, and any other requirements defined during the engineering phase are accurately realized.
The quality of implementation of the designs is critical in ensuring the safety and performance of the membrane containment systems. Yet, as the technology is complex, this implementation can often raise unexpected issues or concerns:
- Design deviations always occur during construction: some have an acceptable or minor impact, while others, more significant, require rectification. It is key that an independent third party be in a position to assess them and define an acceptable action plan, as need be, in order to satisfy all the stakeholders’ constraints ensuring that the technology is preserved: those of the shipyard of course, but also of the ship-owner and the classification society.
- Gas trials are always a truth test: GTT may also provide technical assistance during this key phase where the different equipment (compressors, heater, insulation, etc.) are tested, by performing all the standard operations the vessel will realize during her lifetime (cooling down of the insulation, tank loading/unloading, cargo transfers between tanks, etc).
GTT assistance during construction
GTT’s support during construction is intended to assist the shipyard quality and construction teams to ensure that the containment system is erected properly. Training of the shipyard’s bonding and welding teams, regular patrols, random controls, and specific inspections are typical of the type of service GTT may provide during all the execution phases from the prefabrication stages, to the erection and testing steps of the containment system until the cargo tank commissioning; they are defined with the shipyard in order to maximize the efficiency of the quality control.
Support to quality management
GTT assists the shipyard teams to ensure that the highest quality standards are met during the erection phase.
GTT surveyors’ findings during patrols are systematically shared with the shipyard by way of Daily Patrol Reports (DPR). Regular meetings are also regularly organized with the yard production and quality teams to follow-up on the erection, and on corrective action plans, if any. GTT may even deliver upon request a construction report confirming the suitability of the containment system at delivery.
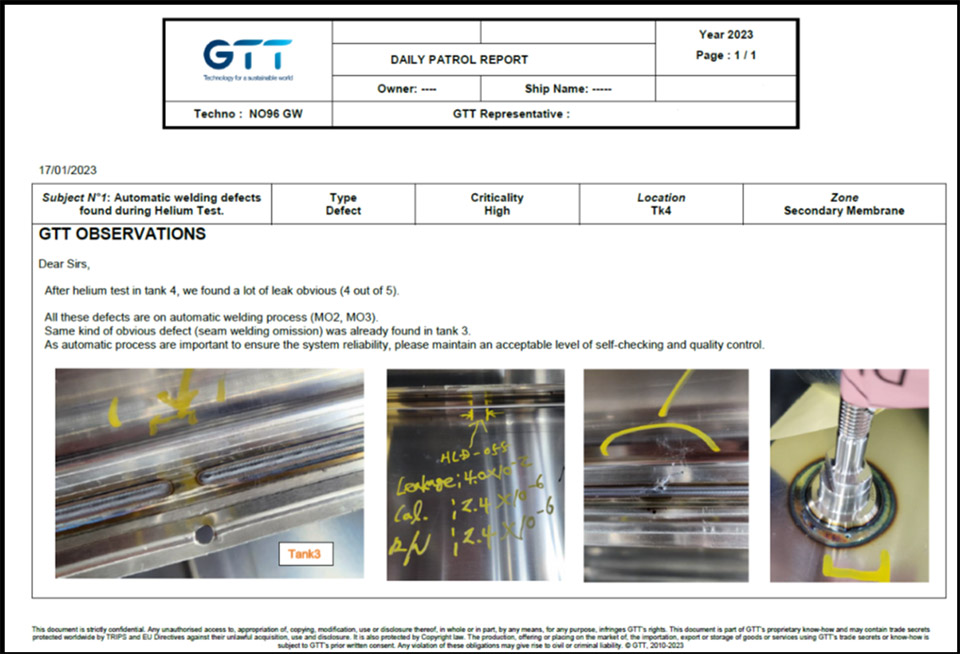
Risk assessment
GTT, as technology provider, benefits from its expert knowledge of the design and the technology to provide independent technical judgements on any issue raised during installation and may also advise on mitigation plans, where available. Depending on the issue at stake, those analyses may be documented through:
• Technical assistance report (TAR) where one specific hull is concerned
• Project Memorandun (PM) where hull series of the same project are concerned
• Shipyard Memorandum (SM) where all hulls in the shipyard are concerned
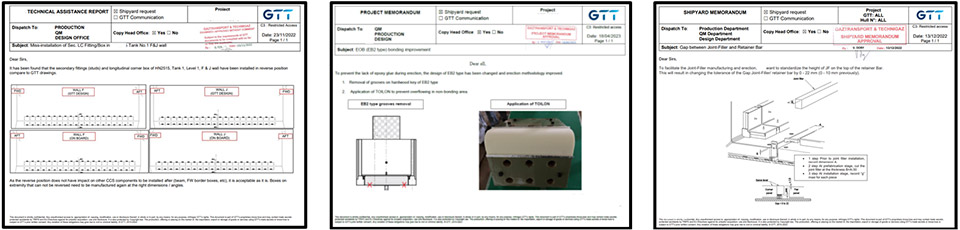
Typical deliverables (TAR, PM, SM) issued by GTT site teams during construction
Where a serious matter arises, potentially affecting the integrity of the tank during construction, GTT may also conduct studies and provide engineering support to define the best technical solution. Such matters may vary from a fire to an electric shutdown, but also over-pressure in the insulation spaces during vacuum tests, or defects of prefabricated CCS components.
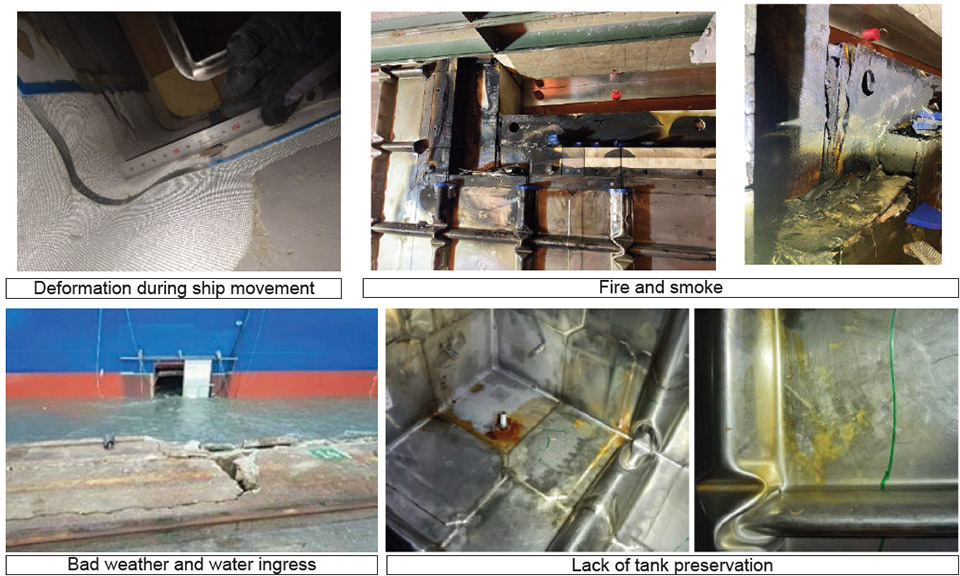
In these instances, where serious repairs cannot be avoided, GTT may rely on its large panel of expertise, including thermal, hydrodynamic, process, structure, design, operational and repair skills, to provide specific analyses to assess the acceptable areas and define tailored-made repairs to be made.
This service take the form of technical reports made available to the shipyards and sometimes the ship-owners to help them address their insurance issues and secure their respective contractual commitments.
Sharing the latest state-of-the-art on GTT technology
GTT membrane systems consist of a complex assembly of composite materials which require specific know-how to be installed in satisfactory conditions. Erection of certain areas might be sensitive, and knowledge of how the technology evolves over time is critical. Therefore, GTT regularly improves its know-how, based both on the evolution of its designs, and its knowledge of the technology overtime, as evidenced by return of experience from vessels in operation.
GTT surveyors therefore are able to provide regular training to the teams of the builder, ship-owner and classification societies and systematically update each party prior to the beginning of construction with the latest learnings and standards available at GTT. This expertise may be shared with shipyards through communication letters.

GTT assistance after delivery
GTT assistance remains available after delivery of the vessel, where unexpected concerns related to the cargo containment systems may arise during ship operations and require further analyses. GTT may provide a wide range of technical advice and support to secure the tank during ship activities, from the monitoring of the tank situation to the issuance of recommendations and to conduct investigations to be performed during first special survey.
Thanks to its wide panel of expertise on its technologies, GTT is able to provide services that maximize ship safety and performance while minimizing the potential impacts on commercial operations or ships downtime for maintenance activities. In particular, if defects are reported during the ship operation, GTT is able to carry out the proper investigations with a holistic approach that leads to a root cause analysis (RCA) report. Each possible cause is systematically analysed based on testing, calculation campaigns and observations. Such assessment is essential for the appropriate understanding of the most probable defect origin to identify the most appropriate mitigation measures, and define recommendations to avoid defect re-occurrence in future constructions. These reports are often required for insurance purposes.
The observations, as well as the outcome of these RCA, with recommended improvements and mitigation measures are transparently shared to the LNG industry in order to secure all the future constructions and vessels in operation. The analyses of all observations are shared through detailed presentations to the relevant parties and where useful, to the industry during the LNG membrane owners forum. Whenever safety of the cargo tanks is at stake, GTT may share its technical analyses to recognized professional associations (SIGTTO, SGMF, etc.) and regulatory authorities (IACS, Flag states, Coast Guards, etc.).
An assistance based on an unrivalled knowledge of GTT technologies
GTT has gradually developed a unique database containing full records from all of its interventions and observations of its systems’ behaviour on vessels in operation. This database fuels mathematical and experimental models, subsequently used to predict likely operation conditions, enabling GTT to anticipate the possible risks of failure, assess their likelihood and justify the technical choices with classification societies.
Thanks to its detailed database, GTT is able to work remotely, identifying and precisely defining the solutions to be implemented, without necessarily involving any alterations to the tank in order to minimize the idle time of the vessel (any intervention involving the tank will put that ship out of service for a minimum of five days).
The maintenance operations are all supervised by GTT’s teams in order to ensure that the quality of the work comply with designer’s requirements and hypothesis and further incorporate the latest maintenance procedures.
GTT continuously upgrades its membrane systems on the basis of the return of experience.
The unmatched track record obtained during the last 60 years is the fruit of constant improvements gathered all along the lifecycle of the vessels starting from the design phase up to scrapping activities. It requires a detailed knowledge of the design of each vessel, a deep involvement in the construction of each cargo containment system layer that only allow to assess very accurately the safety margins and to understand the consequences of each decision on the GTT systems.