The primary barrier of the GTT Mark III Technology is made of 304L, an austenitic stainless steel alloy, 1.2mm thick (Figure 1).
Figure 1: Primary barrier in 304L
The tightness between each membrane is obtained by welding. This operation creates oxides, which must be removed to avoid corrosion (Figure 2).
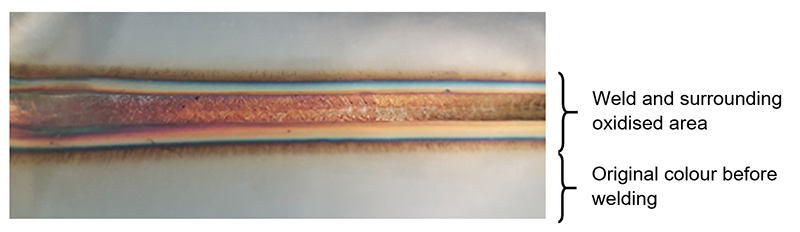
Figure 2: Oxides
Currently, cleaning the weld and surrounding area is a manual operation using a metallic brush.
This operation is difficult and time-consuming (approximately 50km of welds per ship), the ergonomic conditions are poor (vibration, dust and posture), and the repeatability of the operation is uncertain.
With this new prototype, GTT is proposing an alternative to the shipyard in order to:
- Improve the working conditions,
- Reduce the cost by cleaning the weld faster with a single pass,
- Improve repeatability to 100%.
GTT’s Industrialisation Department has defined the process to meet these requirements: the laser pickling robot called OtowoseTM, OTO for automatic and WOSE for Weld Oxyde Sublimation Equipment.
Figure 3 shows that the laser hits the contamination, in this case the oxides, by using powerful and very short laser pulses, which create a micro-plasma and a shockwave which ejects the contamination.
The fumes and the dust are removed by suction through the suction hose located next to the laser impact.
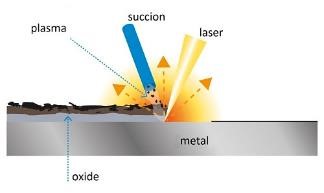
Figure 3: Overview
A closer look reveals a succession of impacts. The aim is to optimise the overlap between each impact to ensure that the oxides are effectively removed. (Figure 4)

The diameter of the spot depends on the laser parameters and the contamination that it will hit. The darker the oxide, the larger the laser absorption and the larger the impact.
Development of the Laser Pickling
To support GTT in this project, two suppliers well known for laser technology have been selected:
- Méliad, a French company specialised in residual stress measurement, non-destructive tests (by using Barkhaussen noise) and surface preparation by laser process.
- CleanLASER, a German company, which develops and produces high-precision laser systems for industrial surface treatment.
To complete this project successfully, it was necessary to identify all the constraints within a containment system, the working environment, space requirements, handling and fixing of the machine. All these inputs were necessary to evaluate the possibility of implementing this type of machine. A second phase of feasibility and robustness studies, which was divided into two sub-phases, was also completed.
- First sub-phase feasibility study.
The aim of this study was to verify the ability of the laser to remove all the oxides in the weld and surrounding area. Using a laser mounted on a 5-axis Robot (Figure 5), welded stainless steel plates were used to find the appropriate laser parameters.
Figure 5: 5-axis robot equipped with the laser head
The samples were then subjected to visual inspection (Figure 6), Scanning Electron Microscopy (SEM) (Figure 7) and salt spray test (Figure 8) to check any start of corrosion. Each test was passed successfully.
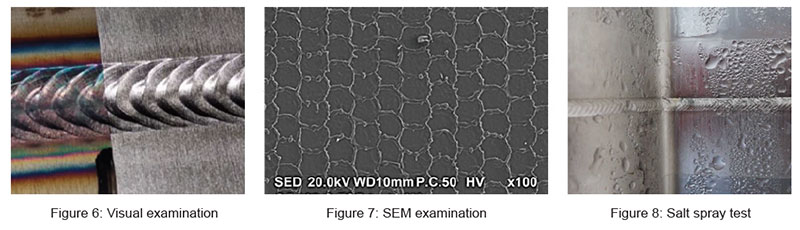
- A second sub-phase “robustness” analysis was carried out in order to assess the positioning tolerance of the laser and to verify that the parameters chosen in sub-Phase 1 provide a satisfactory result for both small and large corrugations of the membrane of the Mark III technology. The samples were subjected to the same test and all were satisfactory.
It took about a year to design the robot, to create its specific software and to manufacture the robot prototype. This prototype was tested on a corrugated membrane and all tests met the GTT specifications.
Figure 9: Front view
The optical system which moves the laser is equipped with a 330mm focal length.
To keep this focal length constant throughout the pickling operation, a specific development was required. Using a sensor, the robot is able to know its exact position without any human assistance.
The laser head is equipped with a suction nozzle to remove the fumes and the dust.
Figure 10: Rear view
The control box is connected to the robot through a specific cable hose that contains the power supply wires and the fibres, which transmits the laser from the generator to the laser head. This cable hose also prevents from an excessive bending that could deteriorate the fibre.
The latch has two functions: to secure the robot on the guide rail and to secure the ignition of the laser.
If the robot does not detect the presence of the rail and the locking handle is not closed, the laser will not emit.
The prototype fully validates the initial objectives:
- The prototype has demonstrated that the cleaning operation is perfectly repeatable with a global speed of 80cm/min (twice the welding speed)
- The operator is not exposed to dust and fumes; his working position is improved as the robot realises the cleaning automatically without any human assistance
- The laser pickling solution is clearly a fast, precise and innovative solution.
Schedule and opportunities
Next step is to begin implementation in each yard.
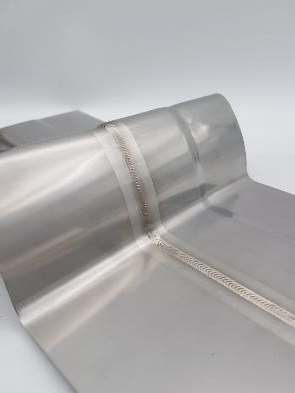
Figure 11: Cleaned Membrane corrugation