Amid rising global energy prices and higher demand, new greenfield onshore projects are running into inflationary headwinds and facing significant challenges to deploy cost-effective LNG storage solutions. This is particularly true when accessing remote areas where logistics are complex and skilled manpower is difficult to deploy. Moreover, as projects become increasingly modularised, slower erection times inherent to stick-built tanks often drive overall project delivery. These observations have led GTT to re-think the conventional industrial scheme of an LNG land storage as a bespoke, fully pre-commissioned, movable asset which could reduce the unit cost of storage and enhance certainty of outcome for project developers. The answer to this question has led to the Modular GST® Membrane LNG (MML for short) storage tank concept. This article describes how membrane technology is key to developing a safe modular system for trans-oceanic transportation.
Concept presentation
The MML tank is an adaptation of stick-built GST® technology, modified with the use of a cylindrical, cryogenic steel outer tank, along with the use of a movable, carbon steel baseplate designed to make the tank light-weight (under 3,500 metric tons), and transportable over remote-controlled Self-Propelled Modular Transporters (SPMT). The idea is to complete its pre-fabrication in a controlled environment with high productivity, and finally deliver to the end user's site on a specialised, semi-submersible vessel, where the tanks are fixed on-deck using a purpose-built welded mounts with load-in capacity for up to three 45,000 m3 MML tanks.
Figure 1: Modular GST®
Main characteristics are:
- Cryogenic steel outer tank - SS304L or 9%Ni to act as a secondary barrier.
- Optimised GST® containment system technology - No thermal corner protection, adapted to cylindrical shape.
- Design adapted for transportation - Dedicated membrane deflection studies and Finite Element Analysis were carried out to validate the containment system with the new carbon steel base plate design.
- Capacity - Range from 10,000 to 45,000 m3.
- Schedule - 17 to 20 months for Ex-Work delivery of 1 tank; 24 to 27 months for 6 tanks.
- Boil-Off Rate (BOR) : similar to standard land storage solutions.
The insulation is composed of Reinforced Polyurethane Foam Panels and a Primary Corrugated Stainless Steel membrane as in the GST® technologies, with some adjustments to match the circular shape of the structure.
Figure 2: Containement system description
The base of the structure is composed of a lattice steel structure assembly filled with a 300mm thick layer of cryogenic rebar reinforced concrete pad, specifically developed to:
- Provide permanent on-site support for the Tank to take on all loads of the tank including operational loads and seismic loads
- Accommodate transportation of the tank as an assembly and to withstand all deflection / motion / acceleration
- Form a thermal barrier against cryogenic temperatures in case of a leak in the tank as there is no thermal corner protection in the tank design
- The concept is validated through Finite Element Analysis.
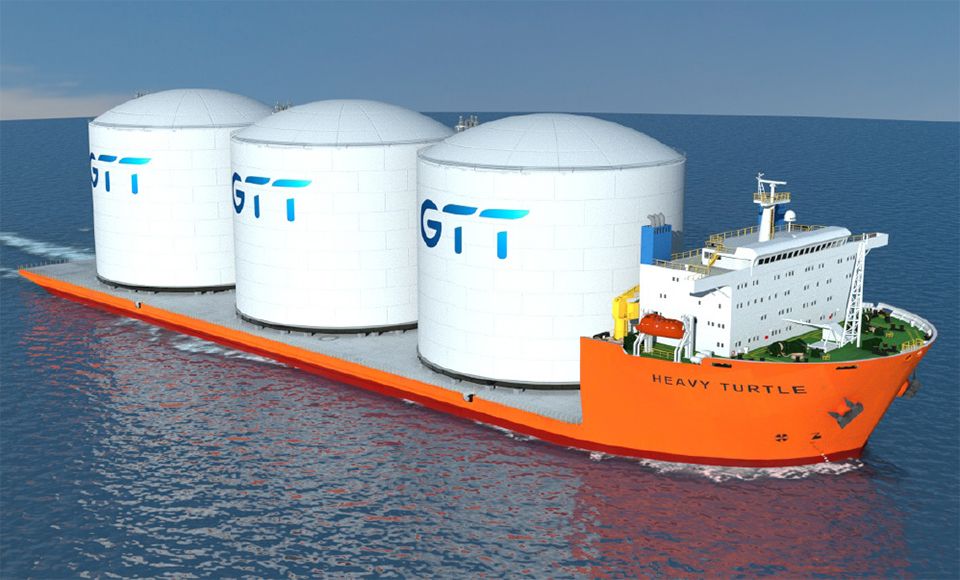
Figure 3: Transportation of MML tanks
Transport
The upper range of tank capacity is constrained to enable the manoeuvring of the prefabricated tank convoy by a heavyhaul road purposely widened to receive it. Dedicated motion analysis studies have been conducted to adapt the design of the modular tank for shipping load cases, and have confirmed feasibility for shipping the 47m diameter and 3500 ton tank structure around the world.
The main impacts of the transportation on the design were:
- Addition of temporary anchors to avoid sliding of the tank itself on the baseplate
- Optimisation of plate thicknesses for walls and bottom to cope with ship motion forces
- Suspended deck is temporarily anchored to allow its installation before transportation.
This study covered the full fabrication cycle from shop fabrication to final site delivery via a combination of trains of SPMTs to achieve the operation.
The transport operation considers a tank without its top maintenance platform, relief and control valves, external piping. These specific
elements shall be delivered separately to be assembled on the end-user and construction site.
Considering a potential application, a transportation study assumed a Asia – North America route with a 3 to 4 weeks duration, for a single, semi-submersible ship transporting three 47m diameter tanks fixed to the ship’s deck via specially designed supports. This study shows that this construction organisation is a pertinent way to proceed and take advantages of significant construction cost reduction, shorter planning and reduced man power on the end user site.
This is mainly thanks to better tank construction conditions such as personnel and supplier availability, less harsh atmospheric condition and parallelisable operation between tank construction and foundation realisation.
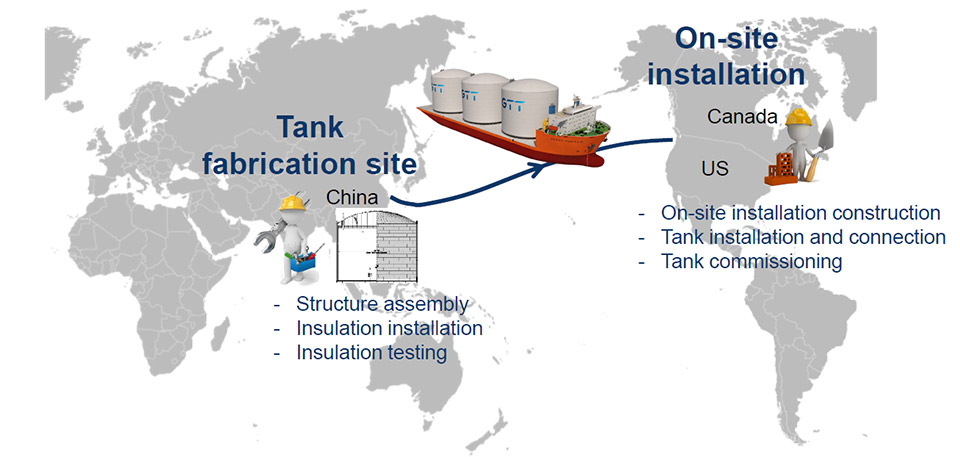
Figure 4: MML tanks routing
This article summarised the feasibility analysis of a new modular, flat-bottom LNG storage tank with GST® technology. The multi-faceted development process exemplifies GTT’s commitment to innovation as a key enabler to unlock challenging markets by bringing substantial benefits through the modularity, scalability, and reliability of membrane technology. While not a single modular LNG tank exists in operation today, GTT’s concept will be the only fully pre-fabricated solution available; resulting in a significant speed-to-market benefit over similar, competitive offers.
Moreover, the aforementioned drive to modularisation among small and mid-scale LNG developers is precipitating a fundamental shift in the way LNG terminals will be constructed in the future, favoring a phased approach to deploy parallel trains to match growing contracted demand. Thus, the adaptation of various storage technologies in step-sized solutions could become the norm rather than the exception in the terminal of the future. This concept should enable GTT’s portfolio to play a key role in future onshore LNG storage requirements.