For GTT membrane technologies, austenitic stainless steels and Fe-36%Ni alloys, typically INVAR®, have been successfully employed as they ensure the required strength, toughness and structural stability at cryogenic temperatures. These two metallic solutions may have reached their limits in an increasingly technologically challenging era for the LNG market.
In 2014, GTT and APERAM Alloys decided to launch a development of a new metallic alloy to be incorporated into GTT membrane technologies.
The Metallic Material & Welding Department of GTT and APERAM Alloys Research Center jointly led this project.
The main objective was to propose a new breakthrough material for the enhancement of existing system competitiveness by providing the best compromise between different properties:
- Enhanced mechanical properties and good toughness at cryogenic temperatures;
- Limited thermal contraction;
- Good formability;
- Corrosion resistance;
- Good weldability;
- Competitive cost.
Laboratory screening
An intensive bibliographic study has been carried out on a large number of academic articles, patents and industrial data. Based on this overview, a laboratory screening has been launched over 12 chemical compositions split into four families, proposed by GTT and APERAM Alloys metallurgists.
Twelve lab castings have been produced and hot rolled to 4 - 5mm thick slabs at the Research Center of APERAM Alloys Imphy.
The hot rolled slabs have been sampled and characterized in order to evaluate the mechanical and thermal properties, toughness and weldability of the produced steels.
Based on this first screening, a promising chemical composition has been identified for the next milestone of the project: the semi-industrial trial.
A new alloy was born; CRYOSTAL®. It is a mixture composed of a significant amount of Manganese, with a Chromium content close to that of a stainless steel as well as a small percentage of Nickel and Nitrogen.
This new metallic solution is not a conventional high-manganese steel but a high-manganese austenitic alloy: even though there is a large manganese content, other alloying elements were also added.
This new alloy meets the technical requirements in term of mechanical properties, ductility at cryogenic temperatures as well as corrosion resistance.
Moreover, impurities such as Sulphur and Phosphorus were limited to improve weldability.
Semi-industrial trial
Two semi-industrial casts of 50kg each have been then produced and cold rolled to a thickness of 1.0mm. Examples of the produced material are shown in Figure 1.
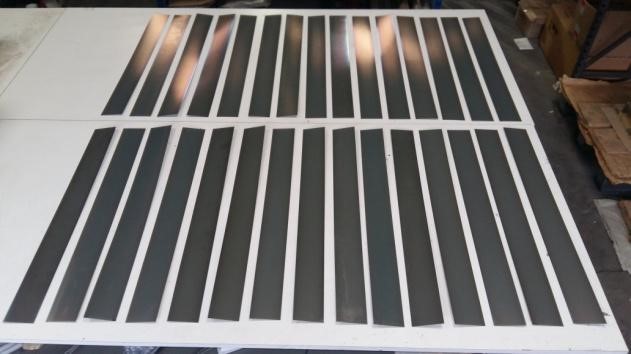
Figure 1 - High Manganese 1mm thick sheets – semi-industrial trial
This step was crucial since as it permitted the verification of the feasibility of the chosen chemical composition and the optimisation of some process parameters before the industrial stage.
Different characterization tests have been carried out in order to evaluate the thermal and mechanical properties, corrosion and weldability behaviour of the elaborated material. The results obtained were very promising and the materials produced showed very interesting properties compared to usual cryogenic metallic materials such as 304L stainless steel and Fe-36%Ni alloy.
The cast is characterized by a high toughness at cryogenic temperature and a lower thermal expansion coefficient compared to stainless steels. In addition, the enhanced mechanical strength and the structural stability at low temperatures and after welding have been highlighted. The weldability of the semi-industrial product has been successfully assessed using Varestraint and Cross-Bead tests.
Industrial product
Based on these encouraging results obtained on the semi-industrial cast, an industrial trial (cast of 120 tons) has been launched in 2019 at APERAM Group industrial facilities. The main objective of this step was to identify potential issues and risks during the casting and the processing of this new material and any corresponding improvements.
The process route used for the production of this new material was similar to other stainless steel products using an electric arc furnace and a continuous casting process. Special management of different parameters was necessary in order to avoid and/or reduce some issues related to the specific chemical composition.
This industrial trial has been a success and two thicknesses have been produced: 0.7mm and 1.0mm.
A new international standard
As mentioned above, this alloy is a new metallic material and it was essential that its chemical composition be recognized in an international standard.
GTT has been working together with APERAM Alloys to register this new material. This work has successfully led to the proposal and the approval of the international standard ISO 23430 dealing with the specification of high manganese austenitic steel thin strips used for LNG tanks on board ships.
C |
Mn |
P |
S |
Al |
Si |
Ni |
Cr |
N |
0.05 max |
24.0 to 34.0 |
0.020 max |
0.010 max |
0.10 max |
0.35 max |
0.50 to 3.50 |
7.50 to 12.50 |
0.05 to 0.25 |
Table 1: Chemical composition of high manganese austenitic alloy (%wt)
Mechanical characteristics
A testing campaign has been carried out in order to characterize the properties of the High Manganese alloy for both 0.7mm and 1.0mm thicknesses.
Figure 2 compares the mechanical properties obtained of our metallic alloy CRYOSTAL® with 304L stainless steel and Fe-36%Ni alloy; both used in GTT technologies.
Our high-manganese alloy CRYOSTAL® shows an enhanced mechanical strength at both ambient and cryogenic temperatures. The relatively lower thermal expansion coefficient allows a non-negligible reduction of the thermal stresses induced by temperature gradient compared to stainless steel.
The fatigue test results on raw material are very satisfactory. Indeed, the results at -163°C are better than the results of both Invar® and 304L.
Corrosion resistance
Conventional high-manganese steels are susceptible to corrosion. Our objective was to develop a new alloy which has a better resistance to general and pitting corrosion than carbon steel, high-manganese steel and Fe-36%Ni.
The measurement of potentio-dynamic polarization curves showed that this new metallic alloy CRYOSTAL® meets this requirement.
For instance, after 1000 h at 55°C and 95% Relative Humidity, no corrosion has been observed.
Weldability
Weldability is a key parameter for the applicability of the material in GTT membrane technologies.
From the early stages of this project, the weldability of CRYOSTAL® has been investigated using Varestraint and Cross-Bead tests. Furthermore, the weldability of the industrial sheets has been verified using different welding processes usually used in GTT technologies such as TIG, PAW and seam welding processes. Figure 3 illustrates some welded CRYOSTAL® samples using different tests and welding processes.
The weldability of our high-manganese alloy CRYOSTAL® has been assessed and no metallurgical issues have been encountered in both homogeneous configuration and heterogeneous assemblies (with 304L stainless steel and Fe-36%Ni alloy). Moreover, the mechanical strength under tensile loads is high.
The fatigue behaviour of the welded specimen is still to be determined.
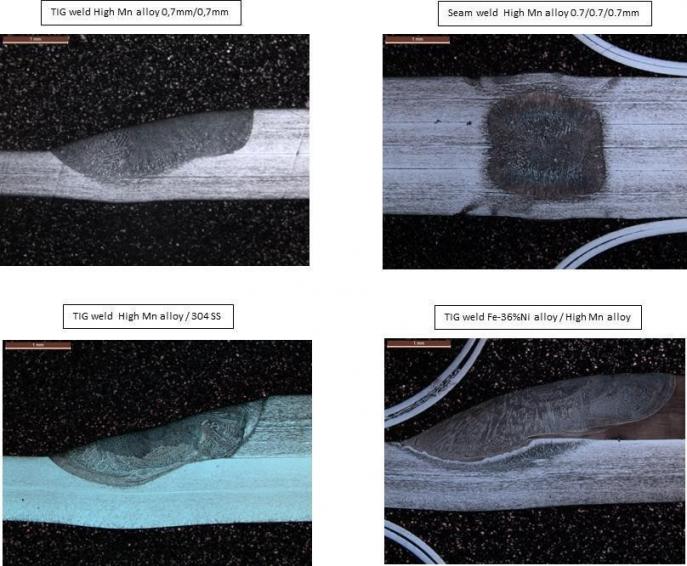
Figure 3 - Illustration of welded samples with High Manganese Alloy
Formability
The forming limit diagram (FLD) of CRYOSTAL® has been determined by means of Nakazima tests in order to evaluate the formability of the material. The obtained FLD is presented in figure 4 and compared to those of 304L stainless steel and Fe-36%Ni alloy.
It can be shown that the workability of the new High Manganese alloy is better than Fe-36%Ni alloy and comparable to 304L stainless steel.
Figure 4 - Forming limit diagram
Moreover, in order to investigate the possibility of using the new High Manganese alloy in a corrugated form (corrugated membrane), 0.7mm thick samples have been shaped using forming tools developed by GTT and already validated for Fe-36%Ni alloy.
The shaping of High Manganese alloy sheets did not show any particular difficulties; which is a promising point for the application of this new material in GTT systems. Figure 5 illustrates the obtained shaped specimens for both high manganese alloy and Fe-36%Ni alloy (for comparison).
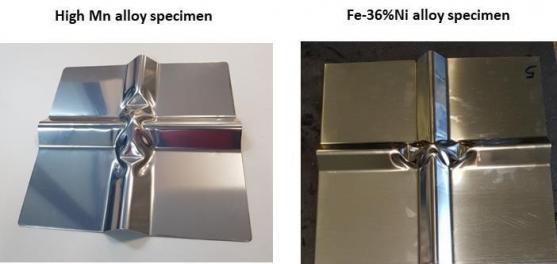
Figure 5: High Manganese alloy and Fe-36%Ni alloy corrugated specimens
Further investigations and testing are still in progress in order to assess the mechanical strength of the corrugation obtained and, if necessary, to further optimise the forming process in such a way as to meet GTT technical requirements.
Regulations
The list of qualified metallic materials to be used in LNG tanks (materials with sufficient toughness at -165°C) according to the IGC and IGF codes is very limited and mainly includes: 9%Ni steel, austenitic stainless steels (304, 304L, 316, 316L, 321 and 347), austenitic Fe-36%Ni alloy and some aluminium alloys.
Since 2015, GTT has been participating actively in the Correspondence Group of the IMO subcommittee on Carriage of Cargoes and Containers (CCC) on the suitability of alternative metallic material for cryogenic service. The working group has reached the validation of the Guidelines for the Acceptance of Alternative Metallic Materials for Cryogenic service in ships carrying liquefied gases in bulk and ships using gases or other low-flashpoint fuels (MSC.1/Circ.1622 ; 2nd, December 2020).
The performance of our high-manganese alloy CRYOSTAL® is in accordance with all the criteria defined in the Guidelines.
Conclusion and perspectives
The development of this new metallic alloy CRYOSTAL® is above all the results of successful collaboration between a designer GTT and a steelmaker APERAM.
It provides very interesting properties at very low temperature. This alloy has higher mechanical characteristics and the cost is independent of nickel prices.
We will continue to assess the applicability of this alloy for future cargo containment systems.
By the middle of 2022, we plan to be able to propose a technology with this high-manganese alloy.