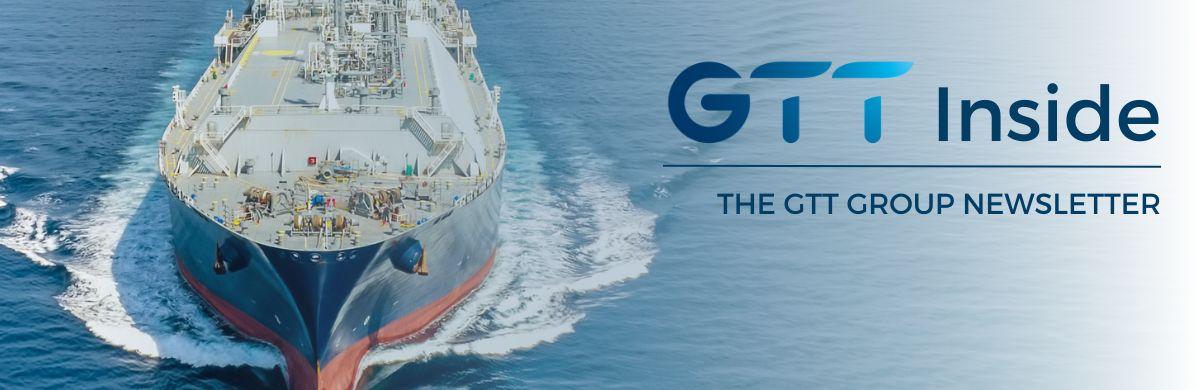
GTT Inside, the GTT newsletter
Message from Philippe Berterottière, Chairman & CEO of GTT
This new edition of GTT Inside reflects GTT’s unwavering commitment to innovation as we address the energy and environmental challenges facing maritime transport today. In a context of tightening regulations and accelerating energy transition, we are delivering practical, high-performance solutions to support our partners on the path to a sustainable future.
This month, we highlight our Recycool™ technology, a cutting-edge recondenser system that optimises boil-off gas (BOG) management on LNG-powered vessels, reducing emissions and enhancing energy efficiency. This innovation demonstrates our ability to combine technological performance with environmental responsibility.
We also explore the arrival of Ultra Large Ethane Carriers and how GTT’s cutting-edge membrane technology is setting new benchmarks in operational flexibility, energy efficiency, and carbon reduction.
Finally, we address the challenges associated with LNG cargoes containing high nitrogen levels – a complex issue that GTT is tackling with proven, robust solutions to ensure the safety and performance of vessels under challenging conditions.
Innovation remains at the heart of our strategy. By investing in tomorrow’s technologies, we continue to strengthen our ability to anticipate our clients' requirements and deliver increasingly efficient and sustainable solutions.
Thank you for your continued trust in GTT.
***
TECH IN FOCUS
Recycool™, a cutting-edge recondenser system
As environmental regulations continue to evolve, improving energy efficiency and reducing emissions from LNG-fuelled ships have become critical challenges. High-pressure ME-GI engines, chosen for their low methane slip and high-power efficiency, are often selected as the main vessel propulsion. However, managing the boil-off gas (BOG) in such high-pressure engines remains complex, requiring a reliable, simple and cost-effective solution.
TECH IN FOCUS
Optimisation of Ethane Transport: A Dedicated Technology by GTT
The demand for ethane transport is increasing, and is expected to grow steadily over the coming years. If flexibility of vessels capable of also carrying different types of cargo, such as LNG (Liquefied Natural Gas), is not required, GTT has developed a membrane technology specifically designed for ethane transportation, leveraging the proven experience of its Mark III system.
PIONEERING PROGRESS
Sustainable And Efficient Ethane Transportation
In the evolving landscape of ethane transportation, GTT has pushed the boundaries with the largest Very Large Ethane Carriers (VLECs) and has also developed and promoted Ultra Large Ethane Carriers (ULECs).
PIONEERING PROGRESS
BOG Line - A simple lever to improve energy efficiency of PRS, FRS and A-PRS
At the forefront of cryogenic system technological advancement for LNG carriers, GTT continuously improves the thermal performance and reliability of its containment systems. To enhance the overall energy efficiency of vessels, GTT also focuses on optimising boil-off gas (BOG) conditions when supplying sub-coolers, reliquefaction units or full re-liquefaction systems (FRS), partial re-liquefaction systems (PRS) or advanced partial re-liquefaction systems (A-PRS).
NAVIGATING THE MARKET
LNG with High Nitrogen content: adapting to a new reality
Over the last decade, numerous liquefaction trains have been commissioned to meet the increasing global demand for Liquefied Natural Gas (LNG). The LNG composition delivered from various terminals differs based on the characteristics of the gas field and the extraction processes used. While LNG typically contains a high proportion of methane, it may also include smaller quantities of heavier gases such as ethane, propane, butane, pentane, and, in some cases, nitrogen (N2).
Previous newsletter