The US shale gas revolution has created a surplus of ethane production which cannot be monetized in the short and medium term in the US alone. This new supply provides opportunities for increased ethane trading between US and Europe, South America, India and most recently China.
In this context, during the past decade, the ethane shipping market has significantly increased and innovative ship designs allowing transportation of larger capacities have been developed. 2014 saw the FID of the first Ethane supply deal adopting the first membrane “large” Ethane carriers with a capacity of 87k, before further increasing in 2018 to almost 100k based on the Mark III containment system. Those vessels also include LPG and Ethylene on the cargo list.
As the VLECs reach the limit of the “VLGC” size, e.g 230m LOA, 36.6m beam to fit most of the world LPG terminals, going larger is possible with Ethane, but the fall-back cargo will need to be changed to another relevant cargo. LNG seems to be the most appropriated one.
With the objective to support this growth, GTT developed through a Join Development Project (JDP) with Samsung Heavy Industries (SHI) a 150k multi-gases carrier able to carry either Ethane or LNG. This new design is a breakthrough solution, not based on a scale up of the previous Ethane Carriers, but based on the already optimized LNG Carriers design. It has been modified to carry ethane as a prime cargo and LNG as a fall-back, in order to give confidence to asset buyer through flexibility of trade.
The hull, with a LOA x B x Td of 274m x 42 x 11.9m has been developed with the objective to access all existing Ethane US terminals, Morgan’s Point, the Netherlands, and Marcus Hook, in addition to major existing LNG terminals.
With the idea to be active players in decarbonisation, SHI and GTT equipped this ship with a MAN ME-GIE (ethane) fuelled high pressure (380 bars) engine which, associated with a shaft generator, is able to reach 16.0 knots while satisfying the EEDI Phase 3 regulation. As an alternative, this engine is fuelable with methane thanks to general similarity with MAN ME-GI type engine. It is however not the case for auxiliary engines, where only methane fuelled engines are available so far on the market. The shaft generator will be in good use at sea to deal with this situation.
To anticipate future gas requirements, pure ethane, C1 Rich commercial ethane, pure methane and LNG have been considered as potential cargoes. Then, state-of-the-art low boil-off Mark III Flex (400mm insulation thickness) technology is applied with an optimized repartition of the foam density, which results in a breakthrough performance of absolute boil-off of ethane carriers. As an example, the absolute Boil off Rate for this 150k Ethane/LNG carrier is lower than the existing 98k Ethane carriers. The bellow figures presents this gain.
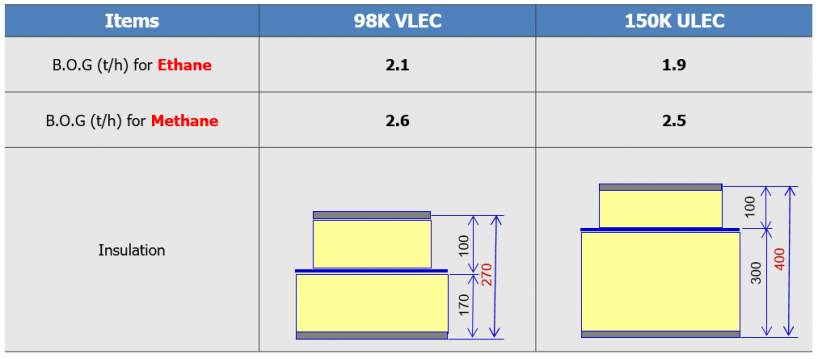
To manage this limited Boil off, the sub-cooling concept, safe and simple, limiting the Boil off Rate by reducing the temperature of the cargo, has been identified as the best solution and selected to equip this innovative ship. The subcooler is optimized for the LNG configuration. For ethane, the subcooler selected is capable to handle 100% of boil off.
GTT developed a smart solution to integrate the sub-cooler into the whole Boil off Gas (BOG) management system. Allowing both CAPEX and OPEX reduction. The GTT solution consists in integration of the subcooler with a low-pressure compressor and a fuel preparation system.
When the ULEC carries ethane, the process becomes the following:
- Fuel preparation system extracts methane rich gas from Natural BOG (NBOG) and supply of that gas to auxiliary engines.
- A Low-pressure compressor extracts NBOG from tanks and compresses it to the pressure required by auxiliary engines.
- Compressed gas is precooled by heat exchange with cold BOG into a pre-cooler heat exchanger
- Then, compressed gas is partially condensed by heat exchange with sub-cooled liquid ethane into a recondensor heat exchanger.
- Partially condensed gas enters C1-sep (liquid-vapour separator), vapour phase, rich in methane (>85%) is supplied to auxiliary engine.
- Methane number is controlled by variation of subcooled liquid ethane flow to recondensor heat exchanger.
- Liquid phase returns back to tanks.
No NBOG is fed to the main engines which allow the removal of the high-pressure compressor from the CHS scope. High-pressure compressor is an equipment requiring high maintenance. Removing it reduces both CAPEX and OPEX.
The main engine is fed with liquid ethane compressed by high-pressure pump and evaporated and heated through a high-pressure vaporizer. This has the advantage of supplying the main engine with a fuel with a stable composition and avoiding the risk of a too high methane content.
When the ULEC carries LNG, the fuel preparation system is in stand-by. The low-pressure compressor supplies NBOG to the auxiliary engines. The subcooler cools a stream of LNG and sprays it into tanks through spraying ramps. The main engine is supplied with liquid LNG through a high-pressure pump and a high-pressure vaporizer.
All main CHS equipment and FGHS equipment were checked for dual compatibility with suppliers and only a few days are necessary to change the cargo from Ethane to LNG making the solution very flexible.
By its versatility, this new generation of ship offers to customers being familiar with the LNG, a real opportunity to enter the Ethane market while keeping the LNG as a fall-back cargo.
As a first reaction, the fall-back cargo of LNG may be seen as too small. Surprisingly, the requirement for trade of such parcel, is needed especially for FSRUs. Therefore a 150k ULEC in LNG trading mode will find competitive advantage compared to this existing 130~150k fleet
A first analysis demonstrates a reduction of at least 20% of the Chartering cost per ton of ethane, compared to a 100k VLEC. This is mainly due to the scale effect.
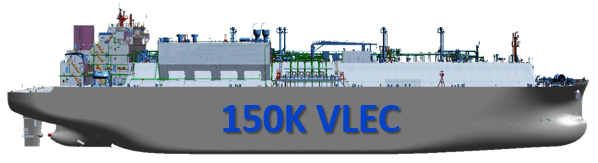