Every day, many ships carry on board a considerable quantity of seawater as ballast over the oceans. Technically, this is needed in empty or partially loaded conditions, in order to maintain seaworthiness, to reach sufficient draft for propeller immersion and to avoid excessive bow slamming.
Taking in big quantities of ballast-water requires investment for the on-board systems and leads to substantial operating costs. In addition, sediments may cumulate at the bottom of the ballast tanks, creating further costs and corrosion problems.
On the environmental side, in addition to the generated emissions, transporting ballast water may transfer harmful aquatic organisms and pathogens when the ballast-water is discharged in the arrival port. The IMO Ballast Water Management Convention is dealing with this major global problem. In most cases today, the compliant solution is by installation of a ballast-water-treatment-system.
However, the best solution is not to use any ballast-water at all: then, the operator is 100% compliant without any treatment or investment.
Solutions with a so-called V-shape hull are generally proposed. The basic idea is to obtain a somewhat higher draft in the design load case, and by that, maintain also a sufficient draft for safe navigation, even when empty.
This principle can be used as far as a draft limit is not attained. For big deadweight carriers (such as Suezmax carriers) it will be impractical.
To overcome these issues, GTT has investigated several concepts and, in their latest approach, has extensively tested their proposed design to reach a fully operable and reliable solution.
The new concept takes full advantage of the specific membrane geometry: the hull lines and the incorporated membrane tanks are designed to match perfectly, and free surface effects of the LNG are reduced when the ship is partially loaded.
GTT Developments
GTT as technology provider is continuously innovating and proposing new solutions to the maritime world. Over the
recent years, GTT has been working on this topic with different Designers and Shipbuilders.
7,500 m3 LNGc design
The view shows a 7 500 m3 single-screw design developed in cooperation with FKAB in Sweden. Such a design is well adapted for small-scale LNG distribution in highly sensitive areas such as the Baltic Sea.
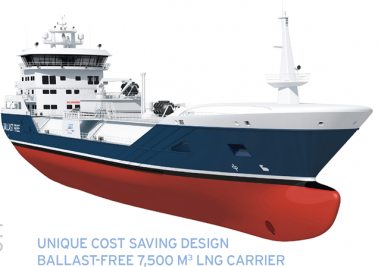
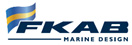
« B-Free » 28,000 m3 LNGc design
Within a Joint Industry Project, a 28k single-screw vessel with two-tanks was designed. GTT Partners were Dalian Shipbuilding Industry Corporation, Lloyd’s Register and Exmar from Belgium. The studies comprised a full sloshing test campaign at GTT, seakeeping calculations made by LR, the vessel design work done by DSIC and interface and operation aspects reviewed by Exmar.
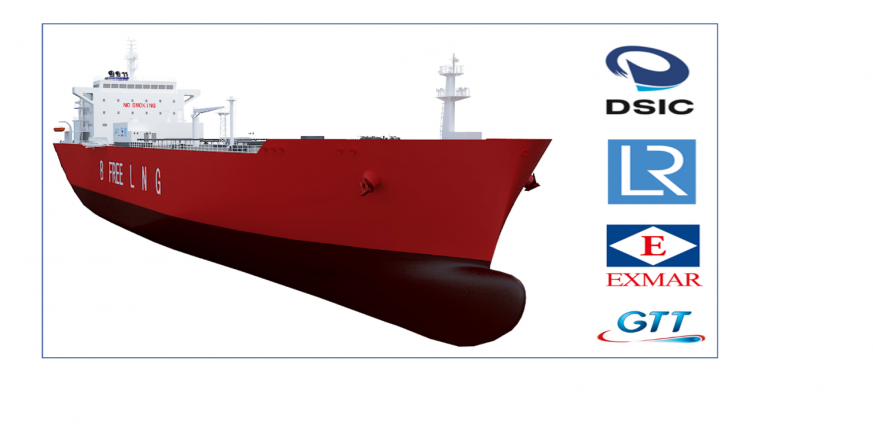
Also, a first batch of seakeeping tests were performed in SSSRI ship model basin in Shanghai.
The outcome and good results are very promising. An AiP was issued by Lloyd’s Register, confirming the design feasibility.
The « Shear-Water » project: extensive testing proves the concept
18,700 m3 LNG Feeder & Bunker vessel « Shear-Water »
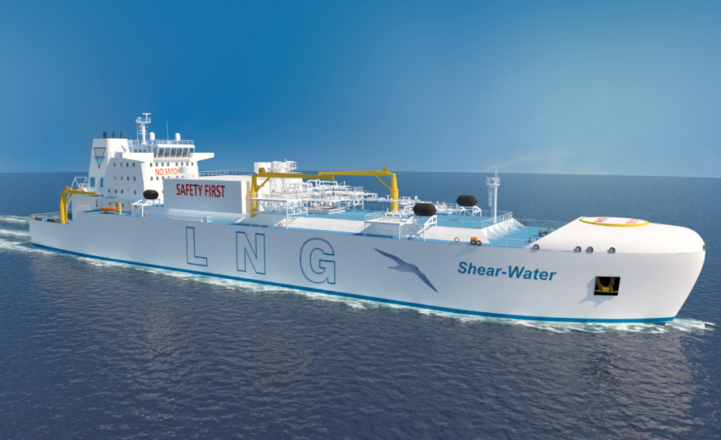
Building on the experience gained on the previous ballast-water-free projects, as well as the recently constructed membrane type LNG Bunker vessels, GTT has developed a new concept for a vessel, which may serve either as LNG bunker vessel or as regional feeder.
The design proposes numerous advantages, such as reduced investment & operating costs, simplified operations, reduced corrosion and a prolonged lifetime.
General Dimensions are : Length x Beam x draft = 141 x 25 x 7.25 m
For a Cargo Volume of 18,700 m3 at a Design Speed of 14.0 knots.
Two identical cargo tanks are provided for simplified operations and a very effective Anti-Roll-Tank system is provided in the vessel’s fore part.
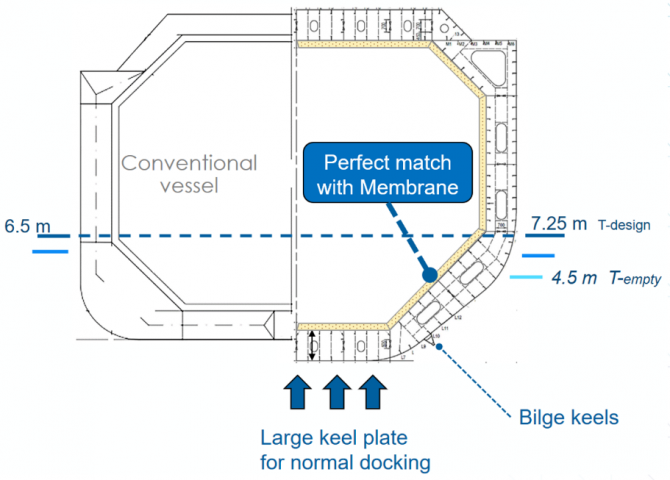
"Shear-wayer" Midship section versus conventional vessel
Compared with the two previous designs, Shear-Water has a twin-screw azimuth propulsion system, increasing the manoeuvring performance and providing a high power reserve in harsh conditions when empty.
Emissions are reduced through lower consumption, on average by a power reduction of over 10% versus a conventional vessel.
Specific issues such as pilot boarding, trim regulation and dry docking were identified, investigated and solutions validated by design.
Especially in coastal trades with frequent calls to major rivers, the benefits are substantial.
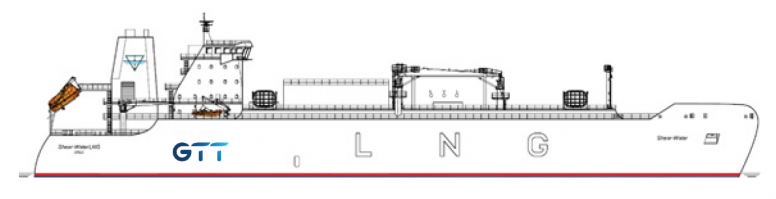
Ship design general aspects
Trim-management is one of the important design issues for such a vessel: careful longitudinal distribution of weight and buoyancy is made by design, and a genuine trim-water system is provided, using some dedicated fresh-water which is permanently on-board. The trim can always be managed in a satisfying, rules-compliant way. The vessel is designed in fully loaded condition at zero-trim and in empty condition with some aft-trim which improves the propeller immersion. In this respect, the use of a bulbous bow shape was not beneficial, also with regard to often changing drafts when operating as LNG-Bunker-Vessel.
The cargo tank filling can be at any level without restriction as demonstrated by the liquid motion campaign conducted.
The operator has just to make sure the vessel’s trim is in the required range - from zero trim to about 1.5 m aft or possibly 1 m forward - and compliant with visibility rules.
Roll-motions are effectively reduced by substantial bilge-keels and further by the Anti-Roll-Tank (“ART” from Hoppe Marine). The installation in the forward part is to say “ideal”, as the space is available without any cargo loss. The ART design is made for the vessel in empty condition but it may also be used in loaded conditions with somewhat reduced effect. The operation of the ART is optional, not “mandatory”, and it uses the onboard trim-water, without losing cargodeadweight.
The question of Parametric Rolling was assessed by HSVA, the Hamburg ship model basin, and can be totally excluded due to the specific hull shape. Effective construction is kept in mind for easy assembly and inspection of the hull structure. The full double structure (bottom, sides and also the upper deck) is mainly composed of void spaces giving substantial advantages compared to a ballasted structure. Docking is made in the same way as any ship: even in empty condition, the vessel can be put in even keel condition to avoid hazardous conditions and the provided large keel plate with supporting side girders assures the required transverse stability even when dry, without further side supports.
The vessel’s Outfitting is proposed on a state-of-the-art basis. Latest knowledge from other LNG Bunker vessels is taken into account for the user’s benefit.
The propulsion system is chosen with Dual-Fuel electric power generation based on three identical gensets and two azimuthing propellers (design provided by Schottel) driven by electric motors. Such configuration gives the best flexibility, high redundancy and best economics for all operations.
The Shear-Water design is evaluated, based on the present propulsion system, to be EEDI compliant for ordering the vessel before 2030. Further improvements may be incorporated over the detailed design process, in close cooperation with the chosen Classification Society.
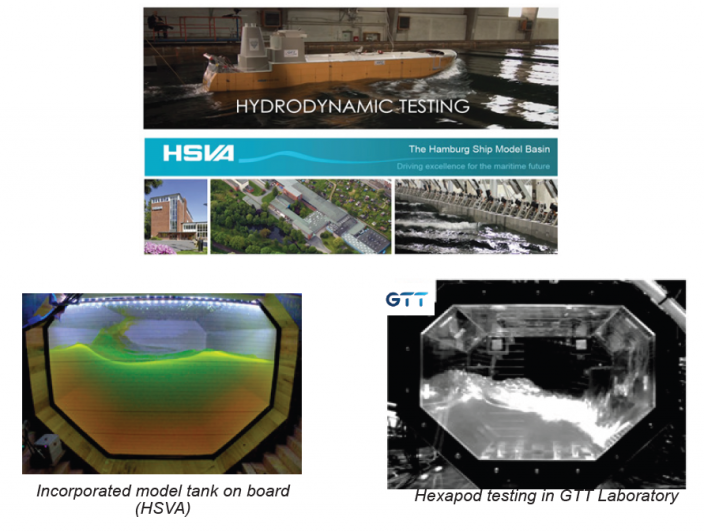
Both campaigns showed results ranging from good to excellent.
Hydrodynamics
The tests were made with a self-propelled model in a scale of 1:18, a length of 7.75 m and a laden weight of 2.8 tons.
Classical calm water tests covered speed-power and manoeuvring. Outcome showed a power reduction of 10-15% for the range 10-14 knots, when considering average values between fully loaded and empty conditions. All compared with a same size & same function, conventional vessel. *
Manoeuvring tests showed results exceeding IMO requirements and expectations. The design shows perfect course keeping, combined with excellent manoeuvring capabilities.
Seakeeping performance was tested in selected sea-sates up to NATO Sea-State 7 (Hs 7.5m). No unusual, excessive or dangerous behaviour in the selected sea-sates has been observed. Observations were similar to other ships in such conditions.
Tests and investigations covered motions and accelerations, rolling including parametric excitation, slamming, Propeller immersion, green water and speed loss in waves.
Course keeping in waves is considered good and the ship was never found to be out of control.
Further tests were made for pilot transfer operations. Comparative tests with & without Anti-Roll-Tank (ART) showed a roll reduction of about 60%.
Additional separate tests were made with the incorporated (single) LNG tank, investigating coupling effects between tank liquid motions and external wave excitation.
Sloshing campaign and optimised Membrane containment system
A dedicated full sloshing campaign was made for worldwide conditions. The obtained good results show no filling restrictions for the chosen containment system Mark III Flex. The insulation foam density is standard 130 and partially 150 kg/m3.
The design Boil-Off-Rate with the above values is 0.165%vol./day.
Cost reductions go with better environment
First estimates show a cost reduction of about 5% in terms of Capex as there is no ballast water system (pumps, valves & pipes, smaller sea-chests) nor treatment system (BWTS) and a reduction of air vents & sounding pipes control.
On the operational side, an annual reduction of around 100-200k$ can be expected thanks to fuel savings due to power reduction when empty (smaller displacement), and a reduction of energy consumption with the lack of ballast water system, no pump power consumption, consumables and spares. Maintenance costs are also reduced by eliminating ballast tank coatings, ballast tank anodes, ballast tank paint and no more maintenance due to sediments. It saves a lot of time due to less cleaning work during dry-drock and therefore savings in docking time.
Last but not least, emissions are reduced by 10-15% compared with a conventional vessel. A good step for a better planet.
Conclusion and Outlook
GTT’s new Ballast-Water-Free design concept has been proven for safe navigation. Beyond this, « Shear-Water » marks a real environmental progress, combined with economic advantages.
The concept may also be used in other ship types, typical candidates could be tankers, container ships and general cargo vessels.
Key operational questions are addressed and Approvals in Principle were obtained from China Classification Society, Det Norske Veritas and Bureau Veritas. Full contractual maturity can now be reached in short time.