GTT continuously invests in research and development to improve its systems and offer innovative solutions to clients. Nevertheless, ensuring seamless project execution is equally important as the success lies in the details.
At the earliest stage, during the bidding process, GTT provides support to its clients to ensure that the ship's specifications regarding the containment system can be met. GTT assists its clients in order to define the most accurate proposal, and provides all necessary preliminary information needed in this respect, from the tank basic design, or the bill of materials to the preliminary boil-off calculations.
Once the project is confirmed, GTT initiates the engineering phase, during which its teams of expert engineers based in Paris work for approximately 9 months to deliver approximately 470 engineering reports and thousands of drawings. Throughout the life of the vessel, GTT continues to ensure the proper implementation of its technologies, addressing any queries raised by shipyards, ship owners, or classification societies on a day-to-day basis and provide all the engineering support on the Cargo Containment System (CCS) that may be necessary.
After delivery of the vessel, GTT offers its detailed knowledge of the containment system’s design and construction, and eventually its specificities, to support maintaining the CCS and monitoring its operational performance.
While membrane containment technologies are by nature complex, the LNG transportation industry is one of the very rare hazardous industries that had fortunately never suffered from a major accident over time.
The vigilance and professionalism of all the industry players obviously accounts for this tremendous result.
GTT is proud to have contributed, through its expert engineering, to the safe growth of an industry that should accelerate its development over the next decade. This article provides a more detailed overview of the engineering capabilities of GTT.
A team of experts dedicated to the CCS design
GTT's cryogenic containment systems are proven to be reliable. This is explained by the resources dedicated by GTT when designing each and every LNGC cargo containment system. GTT's technical division, comprising over 300 engineers, is entirely mobilized to design each CCS in order to meet the ship owner's specifications, the shipyard’s design, the class and flag requirements, and ensure compliance not only with the latest codes and standards but also with the latest state-of-the-art on the GTT’s technologies.
GTT’s engineering capabilities on CCS have been specifically organized to address three concerns:
- safety
- performance
- operational flexibility
Safety of the CCS always remains a major concern
Membrane CCS is one complex technology, which reserves many surprises and sometimes unexpected difficulties. Indeed the CCS is subject to a wide range of stresses caused by hull-induced bending moments, cargo and ballast pressure. For every project, GTT evaluates the stress levels and deformations stemming from the hull and provides guidance on structural enhancements needed to ensure that the CCS operates within a valid acceptable range of stresses.
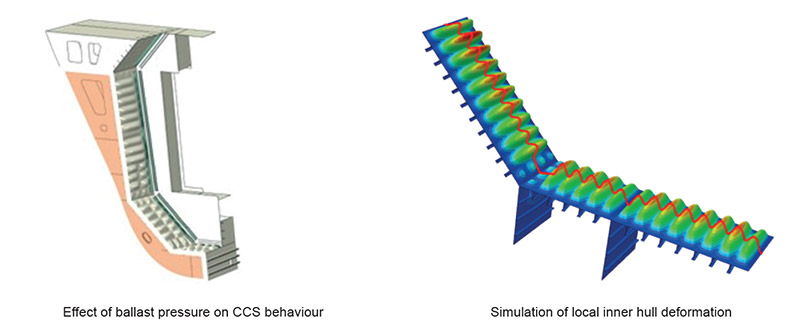
This assessment is at the heart of GTT’s engineering expertise. It comprises a large scope of technical areas, among which, without limitation:
- Review of the steel grades
- Examination of the heating power required for cofferdam heating systems
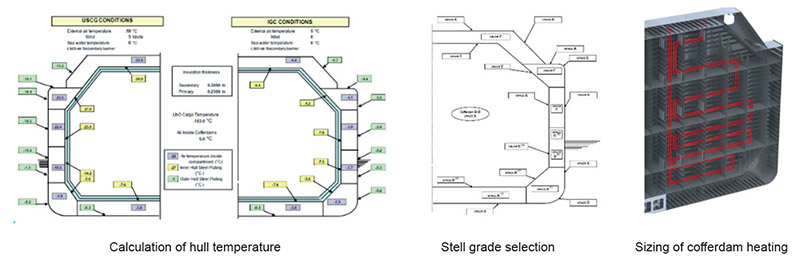
- Sea-keeping analysis for vessel behaviour in various sea conditions, allowing for the determination of the loads that the CCS (including for the avoidance of doubt the pump tower) are likely to experience,
- Ship bending moment and mechanical assessment of the CCS,
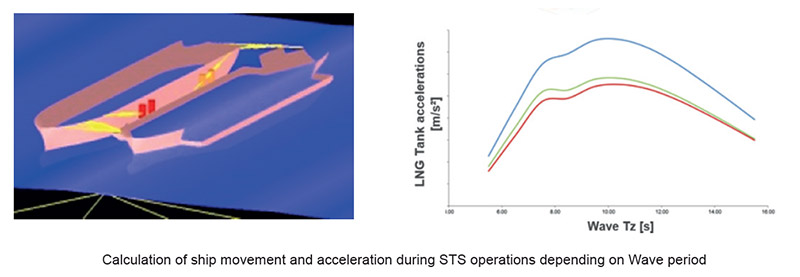
- Sloshing load assessment and tank insulation strength and performance optimisation,
- Detailed panel and component arrangement with required tolerance to ensure correct assembly and correct arrangement to ensure the design safety,
- Detailed design of pump tower tubular structure via the determination of the hydrodynamic and inertial loads by finite elements analysis to assess the acceptability of design with regards to strength and fatigue,
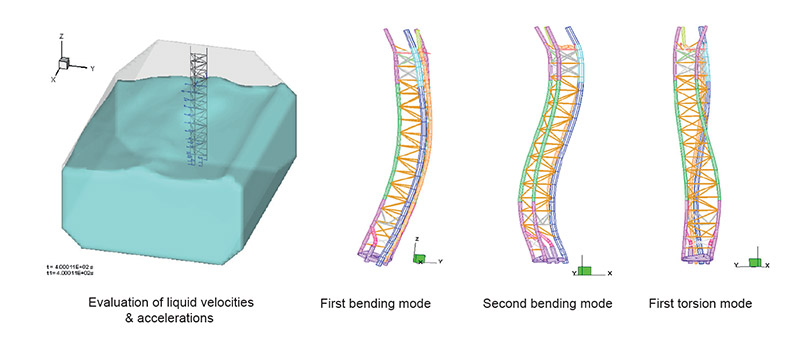
- Vibration analysis to avoid resonance on structural elements,
- Validation of the piping on deck and in the cargo auxiliaries room through stress analysis,
- Design of the nitrogen system, equipment, and instrumentation of the CCS to ensure that the insulation spaces can be safely maintained through inert gas, at the appropriate pressure, under all possible scenarios,
- Proper sizing of safety equipment, such as cargo tank safety valves, insulation safety valves, and Gas Combustion Units,
- Proper procedures to safely manage all critical scenarii described in the Cargo Operating Manual. These scenarios may include Nitrogen sweeping operations, IBS drainage, and IS water drainage, among others.
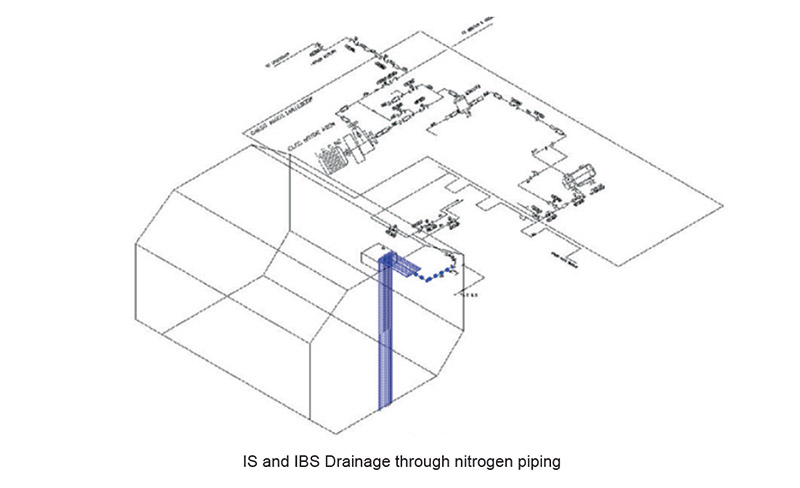
Performance is at the heart of GTT’s designs
GTT conducts an assessment of the Boil-Off Rate (BOR) for the CCS, taking into account the tank geometry, the ship design, and the thermal performance requirements specified by the IGC Code. On this basis, GTT provides a BOR value. Additionally, GTT utilizes the BOR value to determine the appropriate sizing of cargo handling equipment (such as compressors, heaters, vaporizers,etc) that are involved in managing the boil-off.
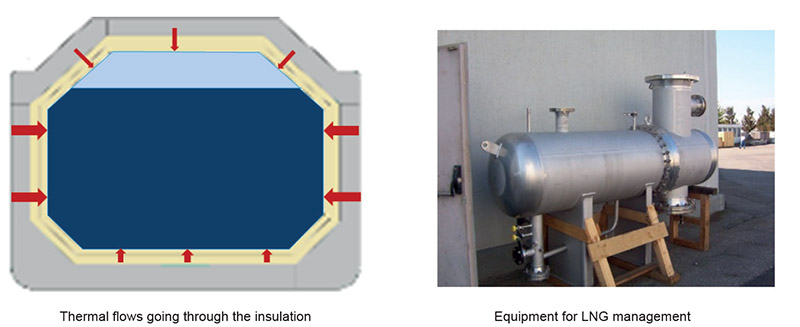
GTT also conducts hydraulic studies to calculate the maximum fluid velocities and pressure drops within critical lines. These studies ensure that the equipment selected by the shipyard, such as pumps, strainers, valves, and pipes, will enable the vessel to meet the performance requirements specified in the shipbuilding specification.
Using sea-keeping analysis and pump characteristics, GTT determines the minimum allowable heel that can be left in the tank before the pump trips. This assessment involves CFD calculations and enables the evaluation of the likelihood of pump tripping for various sea conditions depicted on the scatter diagram. The results of this analysis are further used to alert the crew of any potential risks associated with the operation of the pump.
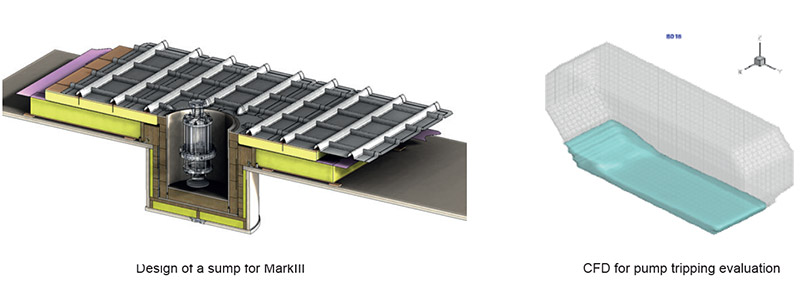
To address the performance of the vessel in terms of loading capacity, GTT conducts an assessment to determine the maximum LNG volume that can be loaded. This assessment takes into account various factors, including the cargo tank geometry, the cargo tank's maximum allowable relief valve setting pressure, and the trim and list conditions required by the IGC code. When a Gas Pocket Crossing System is present, GTT evaluates the increased loading capacity that it provides and conducts a structural analysis to ensure that the crossing pieces are capable of withstanding the thermal and mechanical loads.
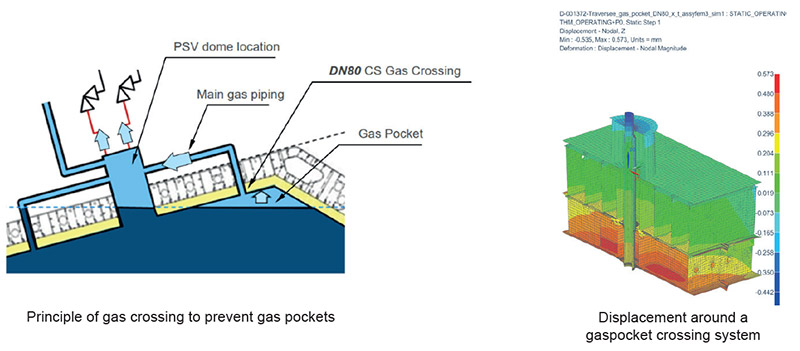
GTT’s designs aim at preserving the widest operational flexibility
GTT has gained extensive knowledge of ship operations through thermodynamic assessment and return of experience at sea. This expertise ensures the safe and efficient conduct of cargo operations and empowers crew members to make informed decisions regarding equipment and system use.
To go beyond the safety requirements of the IGC Code, GTT has developed guidelines on equipment sizing and Fuel Gas Handling System (FGHS) architecture, providing the crew with maximum flexibility in managing day-to-day operations. In addition, GTT offers operators essential guidance to ensure that operations such as commissioning, decommissioning, tank cooling down, tank-to-tank transfer, and one-tank operations are carried out safely and efficiently.
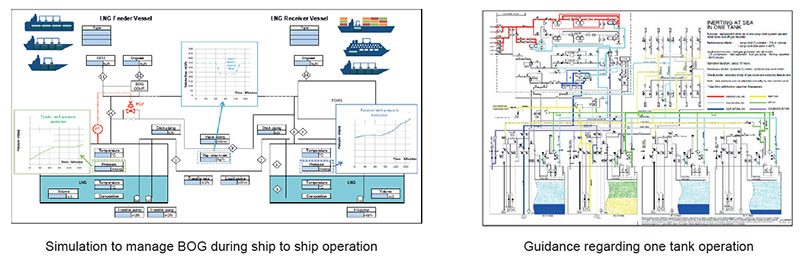
GTT has developed a unique design expertise to continuously meet the market demands in terms of performance and operational adaptability, all the while maintaining system safety.
Through relentless efforts and open dialogue with industry stakeholders, GTT has successfully halved the Boil-Off Rate (BOR) of its technologies within less than a decade. Simultaneously, it has contributed to safely develop new equipment such as FSRUs, FLNGs, arctic vessels or LNG- fuelled ships.
Currently, GTT is actively working on new designs in order to enhance, through innovation and improved flexibility in operations, the thermal performance of LNGCs and align with the International Maritime Organization's emission targets. It also aims at lowering ship costs through innovative solutions and pave the way towards a Net Zero scenario with future synthetic fuels.