In the GTT NO96 technology, the primary and secondary barriers are made of Invar®, a 36% nickel-steel alloy, 0.7mm thick.
To achieve perfect tightness of the primary and secondary membranes, a correct welding is essential.
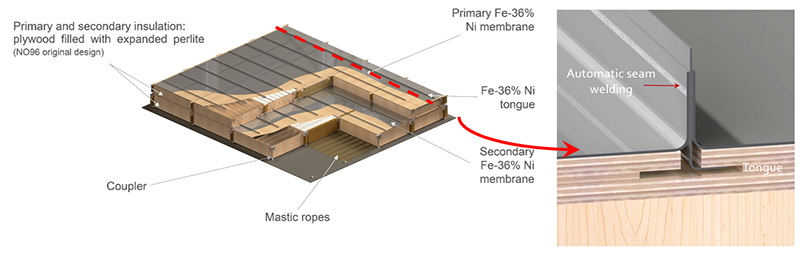
Figure 1: Raised edges on NO96 technologies
The raised-edges (0.7mm membrane / 0.5mm tongue / 0.7mm membrane) are welded continuously over a length of 40 meters thanks to the Resistance Seam Welding machine. On a 174 000m3 NO96 ship, this corresponds to 120km of welding at a speed of 1.6m/min, i.e. 1250 welding hours per LNGC.
In the 1960’s, the first generation of seam welding machine was developed in close collaboration between GTT and ERI, a French engineering company, in order to design and produce all the machines for installing and welding the NO96 membrane. Since then, many improvements have been made and the latest development in operation today dates from 2003.
Figure 2: Actual welding machine in operation
In 2020, GTT has decided to extend the development of welding machine for the installation of our technologies (NO96 and GTT Next1) with the aim of improving efficiency with a faster seam-welding machine and a constant quality control to ensure zero defects.
The seam-welding machine uses a resistance welding process (often used in automotive assembly lines with electrodes) with wheels instead of electrodes in order to perform multiple spot welding along the parts of the assembly.
These parts must be in close contact, so the electrodes (or wheels) compress the upper sheet onto the lower one. A current of several kilo-Amperes flows through the sheets from one electrode to the other.
Figure 3: Resistance spot welding
The heating is due to the Joule effect (E=∫RI²) because of the contact resistances Rc2 and Rc3 (Figure 5). The spot weld appears migrates from the two interfaces until a full weld is obtained (Figure 4).
The weld seam consists of a very large number of overlapping spot welds (see Figure 5). In order to improve the productivity of the welding process, the electrode was replaced by a wheel that exerts a continuous pressure on the sheets to be joined. The current flow is electronically controlled.
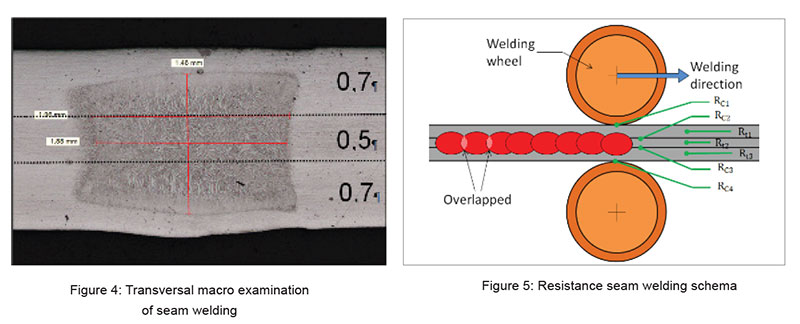
For the success of this project, GTT decided to collaborate with our historical partner ERI.
Technical feasibility (2020)
A comparative study was carried out first. Currently the welding parameters for 0.7/0.5/0.7 Fe-36%Ni raised-edges are:
- 1.6m/min
- 4.2 kA
- 2 hot periods of 20ms and 1 cold (no welding) period of 20ms
- approximately 120daN of force.
The size of the spot welding depends on the value and the application time of current. The current welding machine is supplied by a 50Hz transformer so the minimal period is 20ms. An increase of welding power leads to a bigger welding transformer. An increase of the speed, without reducing the period, leads to a risk of losing the overlapping between welding spots and consequently a loss of tightness (Figure 5).
For this reason, a 1000Hz transformer was chosen, permitting a welding period of 1ms.
Tests at different power levels were carried out with different pressures and periods up to a welding speed of 5m/min. At this speed, the resulting welds met GTT specifications.
For a 5m/min speed, the pressure is still the same and the other parameters are:
- Current between 5 and 7 kA
- 2 hot periods of 6ms and 1 cold period of 6ms.
A longitudinal analysis of the seam confirmed the good continuity of the weld seam.
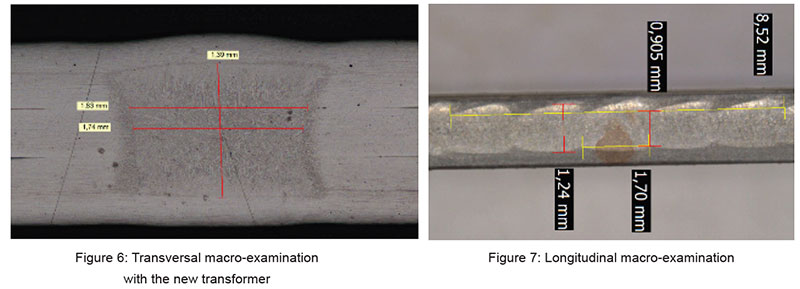
Robustness study in 2021
The second step consisted of studying the process repeatability in terms of tolerance to ensure the onboard welding. With ERI, a campaign on more than one hundred samples was made at different pressures, powers, speeds, and hot/cold periods.
Due to the volume of analyses to be carried out, these experiments took place over several months. A wide range of results were found that met the GTT specifications (the result is shown in Figure 8), indicating that the High Speed Seam Welding process is robust and can be applied in the shipyard.
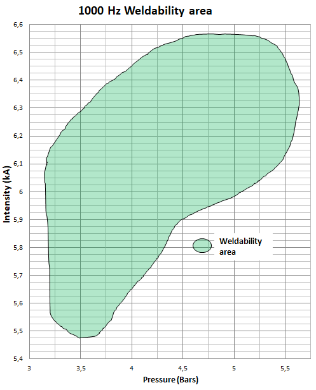
Prototype in 2022
Thanks to the results of the feasibility and the robustness of this technology, GTT decided to make an investment in the development of the prototype. Patents were filed, regarding two main innovations:
- The weld wheels
- The inverter
The weld wheels
On the previous generation of welding machine, the weld wheels diameter was 62mm and after 400 meters of welding, the wheels had to be rectified due to the deterioration of the copper. The temperature during the welding wheels is around 100°C.
Four driving rollers (Ø62mm – Figure 12) and two welding wheels drive the welding head, rotating at the same speed. To avoid the risk of skidding, the welding wheels have to be changed after every 800 metres of welding because they are too small.
Firstly, GTT and ERI have modified the driving system of the welding head to allow free rotation of the welding wheels, which allows variations in diameters between the rollers and the wheels.
The cooling system was also improved with a temperature regulation, better cooling flux, and larger welding wheels to obtain a maximum temperature of 60°C during the welding at 5m/min (5-7kA compared to 4.2kA before).
The inverter
The transformer operates at a frequency of 1000Hz, but the electrical network delivers only 50Hz, so the main purpose of the inverter is to convert 50Hz to 1000Hz and also to control the transformer.
In order to reduce the mass of the inverter, GTT and ERI have developed a customised solution with a positive result: a mass of 4.9kg versus over than 10kg for the current market standard.
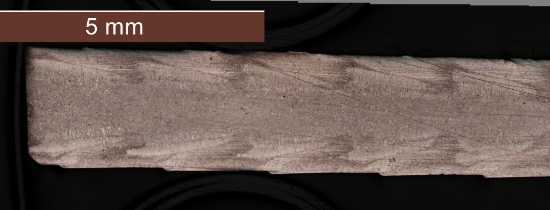
Figure 9: Longitudinal macro-examination of seam welding with the new inverter
OTOSEAM™
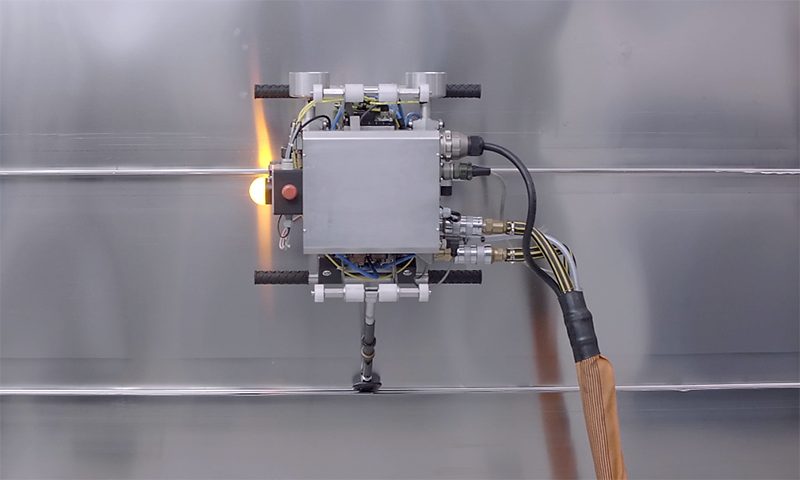
Figure 10: Horizontal position view
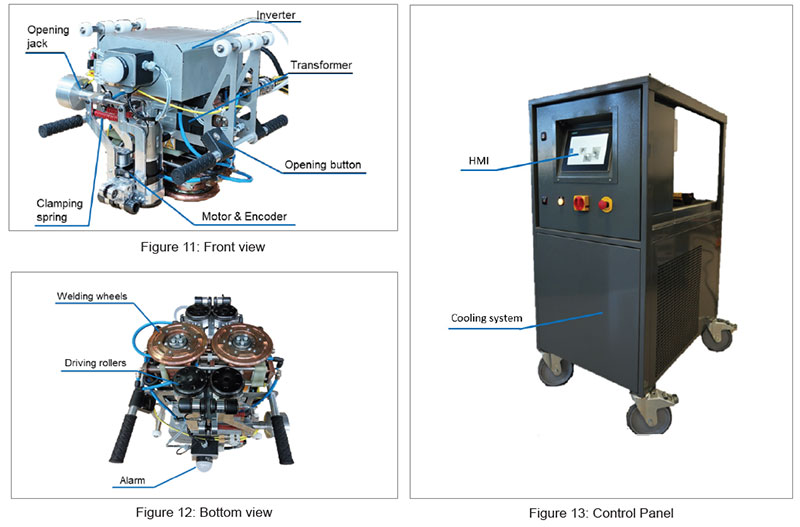
This project proves that it is always possible to improve the efficiency of an existing solution by upgrading with new technologies.
This new generation of seam welding machine called Otoseam™ is now available.
This technology demonstrates a significant productivity gain for the operator thanks to a higher production speed (1.8 to 5 meters/min). Less wheel change means less downtime for predictive maintenance and a continuous quality control through a control of the welding parameters.