LNG is a clean and competitive fuel chosen by major industry players, who have launched significant newbuild projects for LNG fuelled vessels (LFS). Unlike LNG carriers, who do not berth for extended periods for other operations than loading or unloading, merchant ships have longer port stays, during which they sustain electrical loads through on-board fossil fuel powered electrical generators (auxiliary engines). For LNG fuelled ships, electrical load at berth is mainly generated with gas coming from natural Boil Off Gas (nBOG). As the nBOG rate varies with the liquid level in the tank and the electrical demand varies with the commercial operations at port, these two values very rarely match. If nBOG rate exceeds electrical generator consumption, pressure accumulation will occur inside the tank. As it is a key parameter for LNG tanks, GTT decided to carry out experiments to ascertain the LNG behaviour and anticipate such a pressure increase.
A test campaign was performed by GTT last autumn on a 110m3 LNG test facility (GTT LNG Brick with 2 barg maximum allowable pressure).
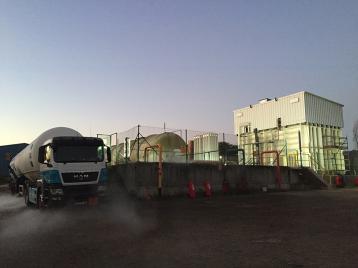
The tests have been specifically designed to simulate the specificities of the real LNG fuelling operation. The impact of the filling level, as well as the ratio between ship fuel consumption and actual boil off rate, has been measured. Pressure rise with the tank fully and partially closed have been investigated.
The LNG used during the experiments contained almost no nitrogen (less than 0.04% by volume) and was representative of the expected LNG loaded as a fuel.
The behaviour of the LNG inside any type of tank is greatly depending on the behaviour of a small layer of LNG at the vapour/liquid interface.
This region has been carefully monitored thanks to a floating device developed by GTT. This floating device is able to measure several temperatures below and above the interface for any liquid level in the tank.
Thanks to this unique device, GTT is able to identify the very specific behaviour occurring at the vapour/liquid interface during the test. The very thin fluid layer (film) forming the interface is constantly vaporizing or condensing the fluid depending on the heat and mass transfer. Heat is mainly coming from the liquid due to the heat transfer through the insulation. Part of the heat is also coming by radiation from the top of the tank. This heat ingress will participate in the evaporation and may limit the condensation. The amount of liquid evaporation is linked to the pressure of the vapour phase. When evaporation occurs, the interface composition is changed. Part of the liquid evaporates (energy balance between heat ingress and latent heat of vaporisation) and the other part is cooled down. In continuous operation at constant pressure, evaporation is stable and the amount is proportional to the heat received by the film and corresponds to the nBOG rate. The nBOG varies with filling level (heat coming from wet and dry surface of the tank), liquid composition and tank shape.
If the vapour flowrate extracted from the tank exceeds the nBOG flowrate, evaporation at film level will increase, bringing the “cold” liquid to return to the bulk. This will lead to the cooling down of the entire liquid bulk, resulting in the reduction of vapour pressure.
On the other hand, if the flowrate extracted is lower than nBOG, evaporation will be limited and the quantity of “cold” liquid returning to the bulk will reduce and may vanish. Heat will accumulate in the liquid just below the film and will form a thermal stratification. This stratification has been measured as being up to 12°C warmer than bulk liquid (closed conditions near 1600 mbarg).
Under low gas consumption, heat accumulation occurs below the vapour interface. Some “warm” LNG is trapped, due to lower density near the interface while, due to low gas consumption, evaporation is limited. This leads to a rapid pressure increase which may jeopardize the ability of the ship to manage pressure accumulation. The consequence of this phenomenon is a pressure increase much faster than expected by homogeneous heat repartition in the liquid (measured up to 12 times faster). At intermediate gas consumption, but still lower than nBOG, the phenomenon disappears due to higher evaporation. The pressure increase is slow and related to the liquid quantity.
Obviously, the behaviour of this layer is linked to the operating conditions of the tank. Filling level and BOG consumption (including hotel load) has a strong impact on the formation of the stratification layer.
GTT has also successfully tested several methods and devices to limit the pressure rise and extend the holding time of the tank by promoting the mixture of the hot LNG layer beneath the interface. There is no direct action on the vapour phase, but the consequence of the mixing is a pressure decrease down to the bulk vapour pressure.
However, mixing methods are increasing heat ingress into the tank so that high intensity mixing may also be detrimental and induce unwanted pressure increase. Obviously, if there is no stratification in the tank, mixing is 100% detrimental. Stratification is therefore one of the key parameters to be detected in a tank before acting on the liquid.
An optimum between a low heat ingress with limited mixing effect and high heat ingress with high mixing effect, depends on many inputs such as LNG tank scale, filling level inside tank, LNG latent heat of vaporisation, gas consumption and parameters such as LNG vapour pressure, gas pressure, LNG density.
Some methods are very promising and GTT can now make recommendations on how to operate LNG fuel tanks at anchor or at berth.