Currently in the doldrums, the Very Large Crude Carriers (VLCC) shipbuilding market is expected to rebound by the end of 2022. In partnership with major shipyards from China and Korea, GTT has developed several designs for long-range LNG-fuelled VLCCs. Having tackled several key technical hurdles, including design, construction and operation, those vessels offer enhanced trading flexibility and reduced OPEX, while taking full advantage of the GTT Mark III system for the fuel tank.
As of today there are 760 VLCCs[1] crossing worldwide oceans. The vast majority are burning conventional fuel oil in vessel’s main engine to propel 320,000 tons deadweight cargo at approximately 13.0 knots. Social pressure and newly implemented regulations have pushed ship owners to look for alternative bunkers in order to reduce emissions of greenhouse gases as well as particles. Among all the available options, LNG fuel has drawn most of ship-owners’ and charterers’ attention. Operational expenditure (OPEX) of VLCCs are significantly reduced when using LNG as fuel, driven by the price difference between long-term contracted LNG fuel and environmental compliant fuel oil.
GTT, in partnership with major shipyards, has carried out technical and financial assessment of LNG-DF VLCCs fitted with a long-range fuel tank capacity. Such long-range design feature allows the vessel to make a return trip with a single bunkering operation in order to optimize voyage duration and to bunker at the cheapest location, and also to minimize series of additional fixed costs such as bunkering fixed fees, etc.
GTT and shipyards have brought their expertise together to integrate this LNG fuel tank with limited impact on the ship design and shipbuilding duration.
Crude oil is the most traded product with a global traded value of around 1,000 billion US dollars in 2019 (The Observatory of Economic Complexity). The Middle East region is the main exporter (37%) while the main importer is Asia (54%).
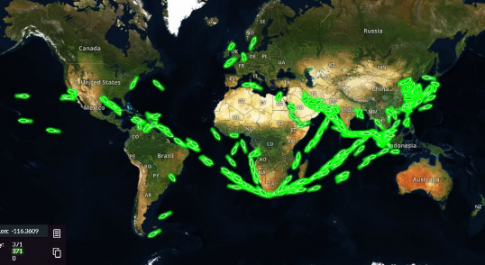
Figure 1 - instant picture of VLCC trades
Source: IHS/MINT
The future of the VLCC market development mainly depends on fleet replacement, ship financing, environmental pressure, charterer’s image and demand for new technology. Considering 20 years vessel lifetime, it is expected that 38 VLCCs per year on average would have to be replaced during the next 20 years.
LNG fuel is quite different from conventional fuel oil bunkers. LNG bunkering infrastructures have known a fast development for the last 3 years, but it took almost a decade to launch 20 large LBVs (LNG bunkering vessels) in the world. The LNG bunker market is more mature in Europe with a wide availability of LBVs. Asia is catching up, especially in Singapore having ambitions to be a major LNG bunkering hub, while the LNG bunker offer in Americas is still limited in particular for large volume.
Table 1 – Required LNG capacity for main VLCC trades
LNG bunker price in Asia is usually more expensive than in Europe or in the USA (less competitive market, less diversity of gas supply) – to the exception of the current recent situation. A VLCC fitted with a large fuel tank capacity can purchase LNG bunker at the cheapest location.
Figure 2 - LNG fuel contracted prices (including bunkering fees)
Source: GTT analysis from Henry Hub, ANEA and LNG Europe
LNG bunker price breakdown includes LNG price, chartering and terminalling fees of LBV. As shown in Figure 3, LNG bunkering cost becomes cheaper when bunkered volume increases, as economies of scale are done 1) on CAPEX & OPEX of LBV and 2) on terminalling fees (who have a share of fixed cost). Hence financial savings can be achieved if single bunkering operation is carried out for a round trip.
Figure 3 - Bunkering cost (without price of the molecule)
Source: GTT analysis
Thanks to potential LNG price arbitrage, cheaper bunkering cost and shorter idle time per round trip, an LNG-DF membrane VLCC could offer savings of up to 1M$ per year[2] . The advantage of having a large fuel tank onboard can maximize the cruising range and the flexibility.
Overall, a VLCCs length is usually between 330 to 340 meters and the maximum deadweight is between 280,000 tons and 320,000 tons. LNG-fuelled VLCCs should keep the same main particulars as conventional VLCCs. The cargo area consists of three lines of five oil tanks separated by two longitudinal bulkheads and two slop tanks.
After looking at several positions, the most suitable location for the LNG fuel tank is in the cargo area in order not to affect the visibility and to avoid weather exposure on the main deck. The tank geometry has been customized to fit in between the two longitudinal bulkheads, close to the mid-ship of the vessel.
This location comes with several other advantages from an operational viewpoint but also from a performance standpoint. Firstly, the mid-ship of the vessel area comes with perpendicular to the sea water’s side shell, suitable for safe mooring of the LBV. Secondly, the LNG bunkering station and the LNG fuel tank are close to each other, minimizing piping distance and related cost. Thirdly, the mid-ship location has a limited impact on the vessel stability behaviour, and enjoys reduced accelerations.
Many parameters of the tank dimensions are then fixed, such as breadth and height. The LNG volume can be adjusted by increasing the tank length according to the targeted cargo capacity and vessel cruising range.
Several VLCC designs have been studied with different tank configurations from 9,000m3 to 14,000m3 and a careful attention to remain above the cargo target of 2.1 million barrels.
Figure 4 - VLCC fitted with 11,000m3 membrane LNG tank
Source: HSHI
VLCCs are amongst the largest ships in the world, with design draft above 20m and moulded breadth (B) of 60m. These very stable ships usually have long rolling period, especially in laden condition. A narrow LNG tank will have a short resonance period. These two period values are distant so sea waves have less effect on liquid inside the tank, as shown in Figure 5. Thanks to this low value of ratio B(tank)/B(ship), sea waves will generate limited waves in LNG tank, resulting in low sloshing loads.
Figure 5 - VLCC roll RAO (Laden and ballast conditions) vs resonance period in LNG fuel tank
Extensive test campaigns on hexapod rigs as seen in figure 6 confirmed these low sloshing loads and enabled GTT to select a typical LNG carrier insulation panels of 130kg/m3 density, which are more cost effective and provide a better boil off rate (BOR) performance.
Figure 6 - VLCC sloshing campaign
Table 2 - Typical VLCC operational profiles sailing back & forth on Middle East - China road
Source: GTT and charterers
The standard foam density in LNG tank containment system results in a limited natural evaporation of fuel from the tank. Based on a typical operational profile covering a round trip voyage from Middle East to China via Singapore as described in Table 2, pressure evolution results (Figure 7) show that the highest tank pressure (around 350 mbarg) will occur at the end of the bunkering operation, when the onboard electrical load is the lowest and the LNG bunker is heated by the transfer. As soon as the bunkering is completed and the vessel starts sailing or running cargo pumps, the fuel tank pressure can be reduced down to 100 mbarg. The pressure in the tank always remains within a sufficient with a margin with regards to the maximum pressure of 700 mbarg (MARVS).
IGF standards require a boil-off gas management system for a LNG fuel tank to allow for pressure holding in tank during at least 15 days (21 days for USCG). By selecting a dual fuel boiler designed to take maximum design boil-off gas from tank, it is guaranteed that an infinite holding time can be safely reached. Operators also have the choice to keep pressure in tank without running boiler. GTT has carried out holding time simulations for different membrane fuel tanks, from 6,000 m3 to 14,000 m3. Hypotheses taken include an 850 kW electrical load and 90% loading level. Calculations demonstrated that for all sizes of LNG fuel tank, a minimum 30 days of pressure holding can be achieved when auxiliary engines run at minimum load.
Compared to a conventional VLCC, there are many advantages in adopting long range LNG fuelled VLCC. Such assets come with a high trading flexibility for the ship-owner and the charterer, able to efficiently operate on chart basis but also spot market. Her large fuel tank capacity is also seen as an advantage for re-sale market. Membrane VLCCs take full advantage of the Mark III system, with high thermal performance and maximum useful volume by locating the tank in the centre part of the vessel.
We have seen that significant operational expenditure savings can be achieved as the owner can bunker at the cheapest location, avoid unnecessary idle time and benefit from scale savings on bunker parcels.
Most importantly, such a design is an immediately available solution to new environmental regulations and social pressure.