The Brussels Express, previously named MV Sajir, was delivered after retrofit by the consortium of Chinese shipyards Hudong Zhonghua (HZ) and Huarun Dadong Dockyard Company (HRDD) to the German ship-owner Hapag Lloyd on April 2nd 2021. This vessel with a capacity of 15.000 TEU is the world first LNG ultra-large containership retrofit. It is now fitted with a 6,700 m3 LNG tank, whose the structure was pre-equipped with GTT’s Mark III cryogenic containment system.
A review of the achievement
What you can see on this picture constitutes a major industrial breakthrough.
But what do we see actually?
A steel structure – or “exoskeleton” – already fitted with GTT Mark III Containment System, hooked to a floating crane - 20 meters high above the sea - and about to be lowered inside the first ever ultra large container vessel to be retrofitted to LNG fuel. This occurred on September 25th at HRDD shipyard near Shanghai.
Take a step back, 4 years ago, when GTT and its industrial partners joined efforts to define and pre-validate the industrial process to convert a 15,000 TEU container vessel.
On paper, the technical challenges were numerous and required studies. Among them, the necessity to find the best approach to meet the following criteria:
- To make the best use of the existing available space on board the vessel.
- To maximise the volume of the tank with the lowest impact on the container capacity.
- To minimise the extent of the structural modifications in order to secure both construction planning and existing integrity of the vessel.
As for all retrofit projects, flexibility and adaptability of the LNG tank to an already existing environment has been a key selection criterion. Attaining a LNG volume of 6,700 m3 in the cargo bay closest to the engine room, the exoskeleton solution offers to Brussels Express an autonomy to be able to sail from Europe to China or vice versa and also optimises the overall design of LNG fuel system by bringing the LNG tank as close as possible to the main and auxiliary engines.
Other tank solutions were evaluated during this pre-project. The type C solution, for instance, was found - early in the process - not adapted / optimal as several tanks were needed to reach a similar volume, all located in 2 cargo holds far from the engine room. Fairly quickly the industrial concept of the membrane exoskeleton was chosen.
Under the exoskeleton concept, the LNG tank is manufactured separately from the vessel, outfitted with Mark III Containment System and then integrated into the vessel.
The difference with the solution called LNG Block™ (refer to the July 2020 edition of GTT Inside for more details) lies on the extent of steel structure. The exoskeleton includes “only” the inner structure of the tank block (on which the containment system is installed) and the external stiffeners which will be connected later to the existing walls or stiffeners inside the vessel. Whereas the LNG Block™ is a structural block as usually built in shipyards, which includes the tank (the block can be a complete section of the vessel for instance). LNG Block™ solution is mainly suitable for new build projects in yards non-familiar with membrane technology but also for future retrofit projects with the possibility to either cut & replace an existing section or lengthen the ship by adding this new LNG section.
The Brussels Express, having a large available and accessible space to hold the tank, was decisive in selecting this approach, as there was no need to cut the vessel. The exoskeleton solution was therefore suitable.
This industrial process is a first of its kind in the long history of GTT projects. Usually the containment system is installed on board during the construction of the newbuilding. There is no integration as such. Hence this new approach faces a lot of specific challenges.
One of them, the design of an exoskeleton capable to accommodate:
- the constraints imposed by the vessel, among others the torsion due to the absence of deck (in comparison to LNG Carriers);
- the requirements of the containment system;
- its own weight during the works and especially during lifting.
Through a close collaboration with GTT, the marine engineering company Technolog, in charge of the tank structural design, made the design of the tank structure as an integrated system to benefit from ship hull strength and then optimized the amount of steel material added to preserve the cargo capacity.
On the list of challenges is the lifting of the exoskeleton. A structure weighing 1,300 tons (steel and containment system material), 20 meters high and 44 meters wide to be lifted from the quay and lowered into the 25 m deep cargo bay 9 of the Brussels Express: this is what we can surely call a special lifting operation!
Special care was taken in the design of the lifting gears as well as verifying the adequacy of the structural design of the exoskeleton for such an operation. The focus was to avoid any permanent deformations for the already installed Containment System (outfitted by Hudong Zhonghua).
In the end, this was almost a routine operation for HRDD, the repair shipyard in charge of the conversion works, which ran the show smoothly in less than 24 hours with a certain mastery. All was then in place for the next challenge: the integration itself.
Before the actual work, GTT worked hard to get more familiar with the naval construction in order to assess / anticipate at best the effect of the integration. But what do we mean by integration?
This operation consists in welding all primary stiffeners of the exoskeleton to the existing ship structure (GTT technology being an integrated membrane tank technology).
The conclusion of those studies helped to define, among others, welding gaps, welding sequences, and welding procedure specifications to reach, before execution, a very good level of confidence together with offering a workable industrial scheme for the Yard. Then from theory to practice, it was time for our partner HRDD to mobilise its welding workforce at the end of September and weld all tank faces. The integration of the tank was completed ahead of the schedule, in six weeks.
Finally, any retrofit project involves by its own nature multiple other challenges ranging from integrating new functionalities into an existing set-up (the control system for instance), through accommodating additional equipment within the sometimes already congested layouts, to the usual deviations between as-built documents and actual dimensions of existing pipe routings.
At the end, all these challenges were managed by the consortium and the main subcontractors despite a difficult context due to the world-wide pandemic.
After the completion of the engine upgrade, the FGHS (Fuel Gas Handling System) integration and the recent commissioning of the entire fuel gas chain, the conversion of this first ultra large container vessel is now completed and the vessel back in service.
Hapag Lloyd has chosen a package of GTT services to accompany this first of a kind dual fuel retrofit. This package includes training through the G-SIM training simulator especially adapted to replicate LNG operations of the Brussels Express. GTT will also provide on board technical assistance during the commissioning of LNG tanks and during the first bunkering operations. If necessary, Hapag Lloyd may use the "HEARS®" service, to obtain 24/7 technical assistance.GTT is proud of having taken part in this atypical project, which demonstrated that the application of the Mark III containment system via an exoskeleton concept is truly feasible; from now on, a realistic alternative exists for bringing LNG to existing ships.
GTT is also working on a new concept of LNG conversion with jumboisation in which the additional container cargo capacity can help monetize the whole retrofit operation.
A ship section with LNG and cargo capacity is built in our LNG Block suppliers in Korea or China. The section is then floated and welded to the existing container vessel. GTT believes there is strong future in both lengthening container ships and LNG conversion.
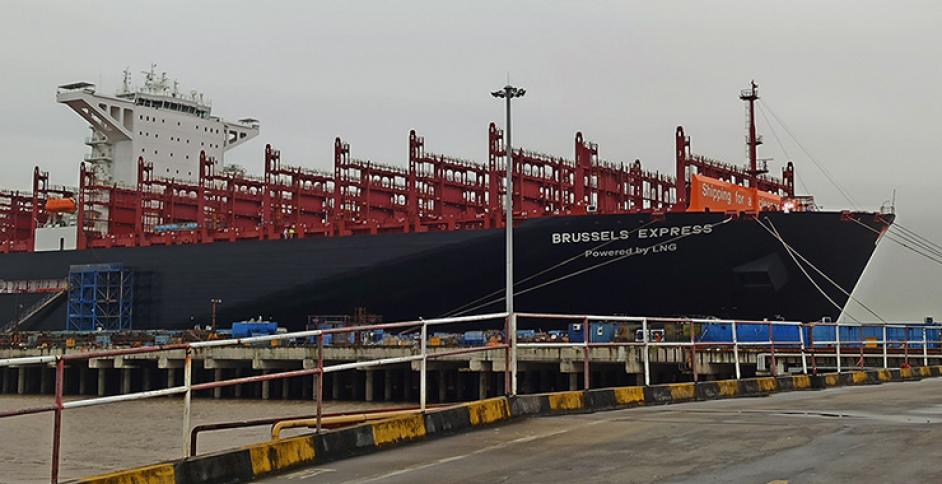