GTT’s innovative 'Ballast-Split' design involves dividing ballast tanks to effectively reduce liquid motion and optimize boil-off rates. By strategically partitioning these tanks, GTT aims to address the challenges posed by partial cargo loading, particularly in the 10 to 40% tank height range where significant loads on the containment system are encountered. Through this article, we delve into the rationale behind the 'Ballast-Split' design, its operational implications, and its potential to set new standards for LNG carrier performance.
LNG carriers and liquefied gas carriers typically utilize ballast water when they are empty or partially loaded. While small vessels like LNG feeders or bunker vessels need to navigate with partial cargo loads, the impact on the containment system from liquid motions in some partially loaded scenarios can present greater challenges compared to fully loaded or nearly empty cargo situations. Typically, when the filling levels of tanks fall within the range of 10 to 40% of the tank height, they can exert significant loads on the containment system, thus requiring increased reinforcements. This condition also applies to ballast-water tanks, which are typically filled to about 70-80% of their capacity.
In scenarios of partial loading, both LNG and ballast-water masses are concentrated in the lower regions of the ship. This configuration increases vessel stability by increasing the metacentric height. However, this heightened stability results in shorter rolling periods but with more pronounced accelerations and consequent higher sloshing loads. To mitigate these challenges, established operational filling limits are adhered to on standard LNG carriers, ensuring optimal containment system performance for maximum cargo delivery. Nonetheless, certain vessels, such as LNG feeders or bunker vessels require the flexibility to operate at any filling level without restrictions.
The question arises: can we maintain standard hull and containment system reinforcements while allowing all tank filling levels?
The concept revolves around maintaining the LNG tank centre of gravity while altering the arrangement of ballast-water tanks. Instead of conventional bottom-to-top ballasting, we propose a reverse method: filling the vessel downward, from top to bottom. This is achieved by dividing the ballast-water tanks into upper and lower sections and initially filling the upper tanks to the required level for achieving the appropriate navigating draft. LPG carriers are already operated in a similar way using what are termed as upper wing and double bottom tanks. With the Ballast-Split design, GTT is proposing now a comparable concept for LNG Carriers.
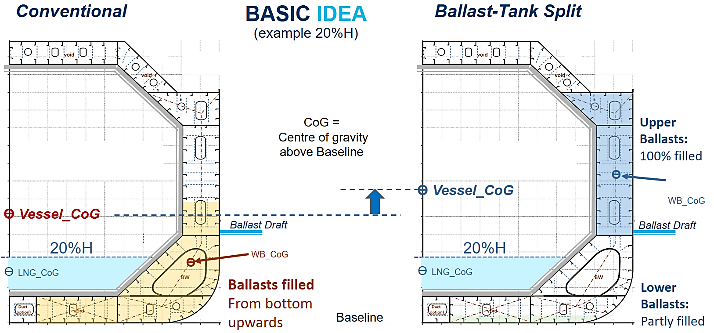
Schematic layout depicting the separation of ballast-water tanks into upper and lower parts.
This modification results in a vessel with a slightly elevated global centre of gravity, leading to a reduced metacentric height and subsequent dampening accelerations. This decrease in accelerations proves advantageous, particularly in mitigating severe cases of liquid motion. Consequently, we achieve a vessel design free from filling level restrictions. Moreover, the diminished sloshing loads on the membrane system permit a reduction in hull and containment system reinforcements compared to conventional designs, thereby lowering the boil-off rate and shipbuilding costs. Determining the necessary number of divided ballast tanks requires early investigations during the project design phase. Effective collaboration between GTT and the shipyard or designated designer is crucial to maximizing operational benefits with minimal design impact. The modified vessel stability poses no adverse effects. However, implementing this ballast-split solution requires a higher number of ballast tanks, resulting in some additional piping and corresponding valve arrangements. In spite of adding ballast-tanks, the vessel cost is expected to be similar or lower, due to potential gains for the cargo containment and reduction of steel scantlings.
Example: a new concept of 30k m3 LNG Feeder vessel proposed by GTT
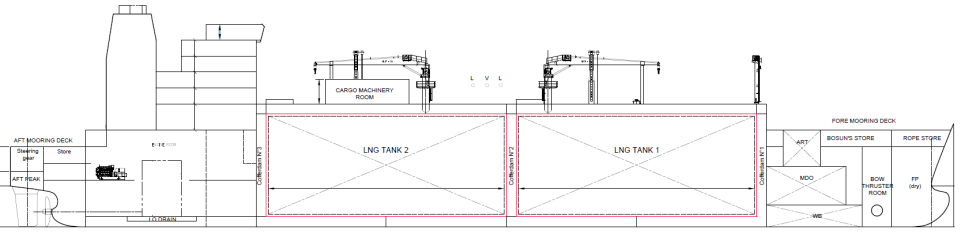
New GTT 30k m3 LNG Feeder design
GTT has recently designed a new 30k m3 LNG Feeder vessel with two identical cargo tanks equipped with Mark III Flex. The ship has been designed for all LNG filling levels. In order to minimize hull and containment system reinforcements, the ballast-split principle has been applied.
The benefits of the new design are highly favourable with the implementation of the ballast-split solution significantly mitigating sloshing activity. The design’s efficacy has been confirmed through validation under North Atlantic conditions across all filling levels, utilizing solely standard foam reinforcement (without the need for high-density foam).
Employing 100% standard foam translates to reduced costs and improved Boil-Off-Rate (BOR). Additionally, the adoption of two identical cargo tanks contributes to cost efficiency and streamlined operations.
Similar promising findings have emerged from the application of these principles in the design of a new GTT 12k m3 LNG Bunker Vessel. These results affirm the practical interest of the initial concept.
It is worth noting that the ballast-split principle holds potential applicability beyond LNG tankers, extending to other liquid-gas or various tanker and offshore unit types.